Loading ...
Loading ...
Loading ...
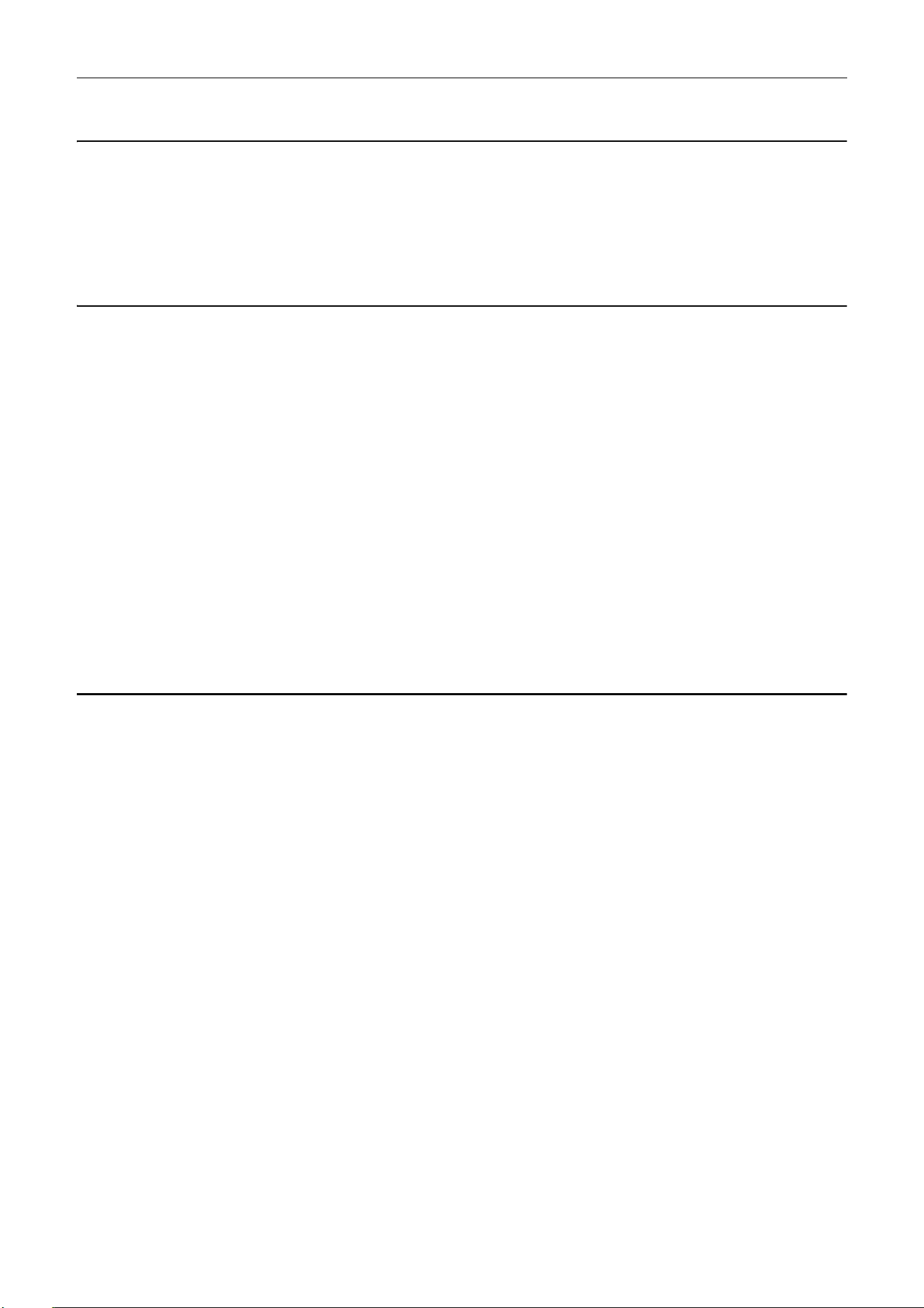
SINAMICS G120C
List Manual (LH13), 04/2014, A5E33840768B AA
479
4 Faults and alarms
4.2 List of faults and alarms
A01590 (F) Drive: Motor maintenance interval expired
Message class: General drive fault (19)
Reaction: NONE
Acknowledge: NONE
Cause: The selected service/maintenance interval for this motor was reached.
Alarm value (r2124, interpret decimal):
Motor data set number.
Remedy: carry out service/maintenance and reset the service/maintenance interval.
F01600 SI P1 (CU): STOP A initiated
Message class: Safety monitoring channel has identified an error (10)
Reaction: OFF2
Acknowledge: IMMEDIATELY (POWER ON)
Cause: The drive-integrated "Safety Integrated" function on processor 1 has detected an error and initiated a STOP A.
- forced checking procedure of the safety shutdown path on processor 1 unsuccessful.
- subsequent response to fault F01611 (defect in a monitoring channel).
Fault value (r0949, interpret decimal):
0: Stop request from processor 2.
1005: Pulses suppressed although STO not selected and there is no internal STOP A present.
1010: Pulses enabled although STO is selected or an internal STOP A is present.
1011: Internal fault for the pulse enable in the Power Module.
9999: Subsequent response to fault F01611.
Remedy: - select Safe Torque Off and de-select again.
- carry out a POWER ON (power off/on) for all components.
- replace Power Module involved.
For fault value = 9999:
- carry out diagnostics for fault F01611.
Note:
STO: Safe Torque Off
F01611 (A) SI P1 (CU): Defect in a monitoring channel
Message class: Safety monitoring channel has identified an error (10)
Reaction: NONE (OFF1, OFF2, OFF3)
Acknowledge: IMMEDIATELY (POWER ON)
Cause: The drive-integrated "Safety Integrated" function on processor 1 has detected a fault in the crosswise data
comparison between the two monitoring channels and has initiated a STOP F.
Fault F01600 (SI P1: STOP A initiated) is output as a consequence of this fault.
Fault value (r0949, interpret decimal):
0: Stop request from processor 2.
1 ... 999:
Number of the cross-compared data that resulted in this fault. This number is also displayed in r9795.
2: SI enable safety functions (p9601, p9801). Crosswise data comparison is only carried out for the supported bits.
3: SI F-DI changeover tolerance time (p9650, p9850).
8: SI PROFIsafe address (p9610, p9810).
9: SI debounce time for STO (p9651, p9851).
1000: Watchdog timer has expired.
Within the time of approx. 5 x p9650, alternatively, the following was defined:
- Too many signal changes have occurred at the F-DI.
- Via PROFIsafe, STO was too frequently initiated (also as subsequent response).
1001, 1002: Initialization error, change timer / check timer.
2000: Status of the STO selection for both monitoring channels are different.
2001: Feedback signals of safe pulse suppression on the two monitoring channels are different.
2002: Statuses of the delay timer SS1 on both monitoring channels are different (status of the timer in p9650/p9850).
2003: Status of the STO terminal for both monitoring channels are different.
6000 ... 6166:
Loading ...
Loading ...
Loading ...