Loading ...
Loading ...
Loading ...
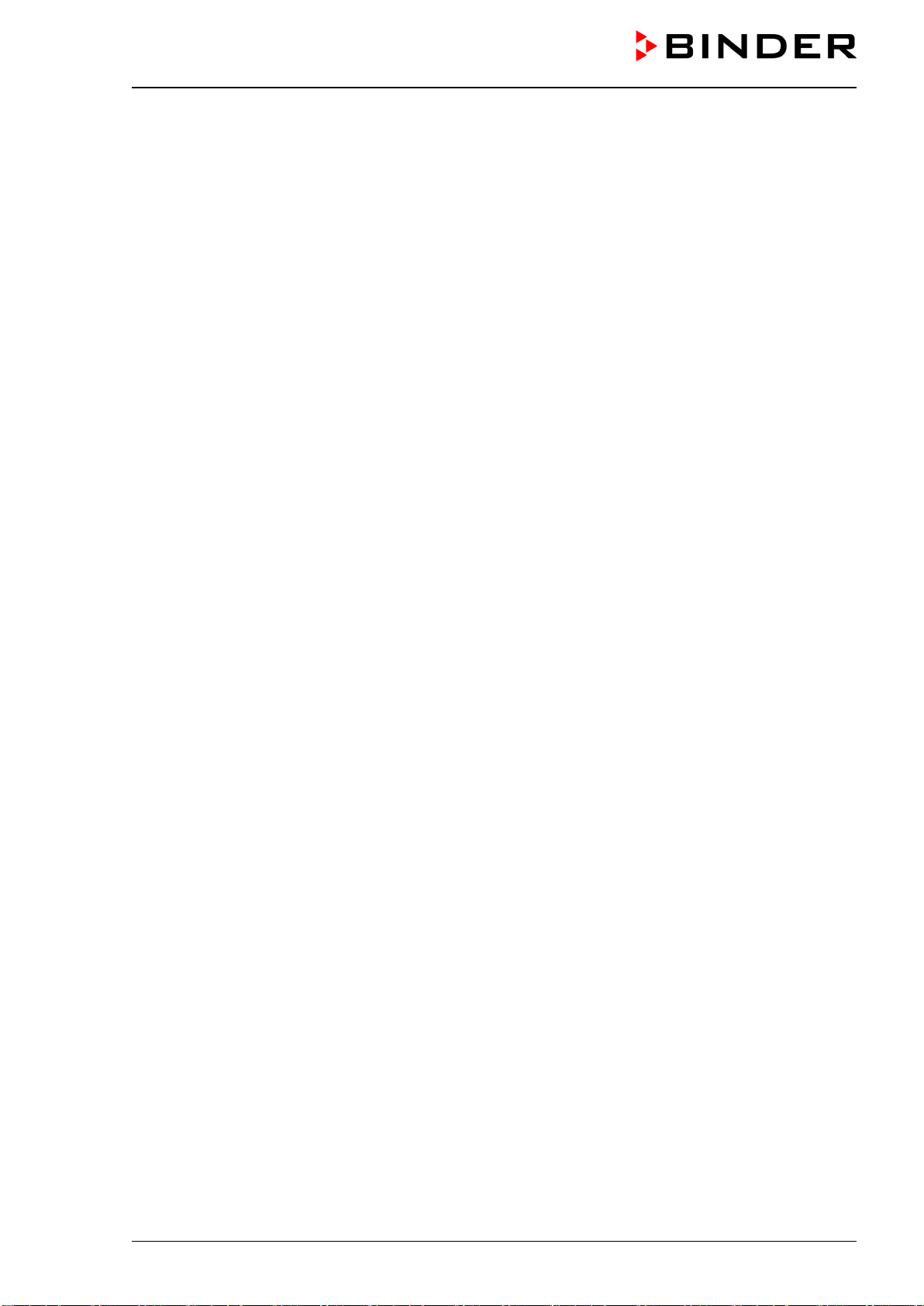
VDL (E3.1) 10/2020 Page 38/196
The outer surface of the preheating chamber (category 3) can reach a maximum of 195 °C.
Normal operation when used correctly: Even without taking into account the pressure control, which is
also effective in practice, there is no ignition source during the drying process. This also applies in the
event that the system is ventilated before the drying process finishes.
Fault: Incorrect loading with inadmissible solvent with a too low ignition temperature: Due to the vacuum,
there is no ignition source during the drying process. The drying process could safely be ended. In order
to cancel the drying process, it is the chamber must first have cooled to room temperature before ven-
tilation and opening (chap. 9.9.4).
• Taking into account the volume dependence of the auto-ignition temperature
The surface temperature is not to exceed 80% of the auto-ignition temperature of the gas or fluid, meas-
ured in °C.
Action: The safety margin of 20% of the auto-ignition temperature. is sufficiently large (EN1127-1:2019).
• Safety pressure monitoring with heater release by pressure switch
There is no explosive atmosphere in a vacuum. The heater is only released starting with a pressure
threshold of 100 mbar.
There is thus always a vacuum ≤ 100mbar during drying.
The protective measure of ignition source monitoring provides redundant safety during the drying pro-
cess: There are no hot surfaces at a pressure > 100 mbar, and, when used correctly, after the heater is
released the hot surfaces are always below the auto-ignition temperature of permitted materials.
• Sweeping the area for electrical equipment, the preheating chamber, and the controller housing
(triangle instrument box) with compressed air
The area for electrical equipment, the controller housing and the preheating chamber between the inner
and outer chamber where the heater is located, are protected against penetration of explosive atmos-
phere by a technical ventilation system.
Before each start-up, sweeping takes place with maximum overpressure. When the chamber is in oper-
ation, it is continuously swept with a minimum overpressure of 25 Pa (recommendation: >40 Pa). The
user must monitor the pressure on the manometer on the chamber front, especially when loading and
removing the loading material This reliably prevents explosive atmosphere to reach electrical or elec-
tronic parts of the VDL safety vacuum drying oven or at the heater (protection against solvent-containing
ambient air).
The compressed air supply line provided by the operator must be equipped with active monitoring of the
defined inlet pressure (2 bar).
• Heater shutdown in the event of component failure
In case of failure of the controller Pt100 temperature sensor or the heater Pt100 temperature sensor.
The heater is turned off. On the controller an alarm message is displayed.
• Measures for lacking / incorrect maintenance / adjustment / sensor drift
Proper maintenance requires that the controller sensor is correctly adjusted. The safety temperature
limiter (TL) provides sufficient safety against heating sensor drift.
Regular adjustment intervals for the controller sensor (annually) are specified (chap. 26.3).
• Prevention of electrostatic charges / grounding plan
All chamber components are at a common potential. The interior parts of the chamber are grounded.
The outer powder-coated housing plates have a layer thickness of 60 µm and are connected with the
earth potential via the protective conductor connection.
A detailed grounding plan for the VDL, the pump module, the pump and the installation and loading area
is provided, all components are prepared accordingly for grounding: Connections are available to ground
the device and accessories. Achieving equipotential bonding according to the grounding plan of the
manufacturer is mandatory, see operating manual chap. 6.8.
Loading ...
Loading ...
Loading ...