Loading ...
Loading ...
Loading ...
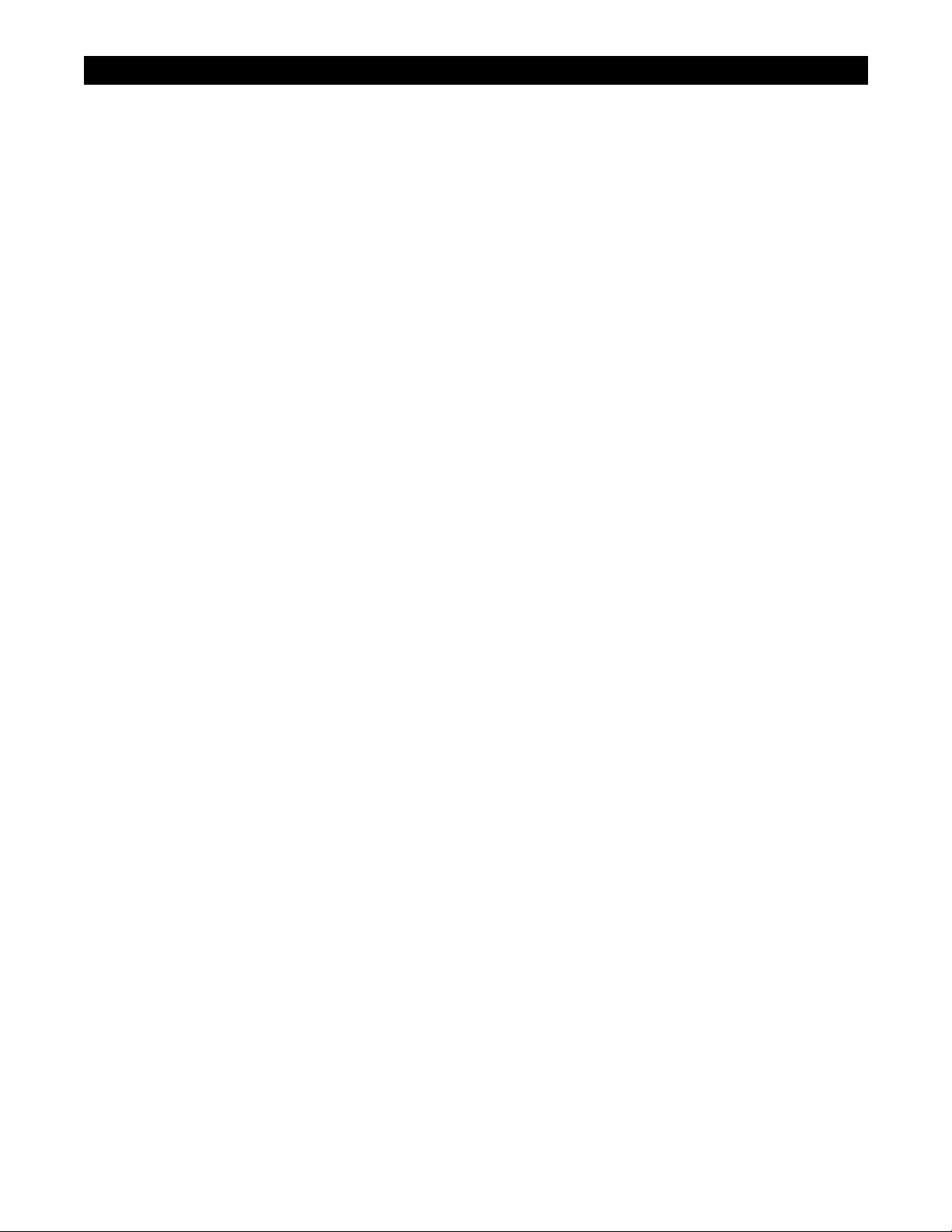
NOTE: Only positive sealing check valves should be
used in submersible installations. Although drilling
the check valve or using drain-back check valves may
prevent back spinning, they create upthrust and water
hammer problems.
Check valves are used to hold pressure in the system
when the pump stops. They also prevent backspin,
water hammer, and upthrust. Any of these can lead to
early pump or motor failure.
A. Backspin - With no check valve or a failed check
valve, the water in the drop pipe and the water in
the system can flow down the discharge pipe when
the motor stops. This can cause the pump to rotate
in a reverse direction. If the motor is started while
it is backspinning, an excessive force is placed
across the pump-motor assembly that can cause
impeller damage, motor or pump shaft breakage,
excessive bearing wear, etc.
B. Upthrust - With no check valve, a leaking check
valve, or drilled check valve, the unit starts under
a zero head condition. This causes an uplifting or
upthrust on the impeller-shaft assembly in the pump.
This upward movement carries across the pump-
motor coupling and creates an upthrust condition in
the motor. Repeated upthrust can cause premature
failure of both the pump and the motor.
C. Water Hammer - If the lowest check valve is more
than 30 feet above the standing (lowest static)
water level, or a lower check valve leaks and the
check valve above holds, a vacuum is created in
the discharge piping. On the next pump start, water
moving at very high velocity fills the void and strikes
the closed check valve and the stationary water in
the pipe above it, causing a hydraulic shock. This
shock can split pipes, break joints and damage the
pump and/or motor. Water hammer can often be
heard or felt. When discovered, the system should
be shut down and the pump installer contacted to
correct the problem.
INSTALLING THE PUMP WITH POLYETHYLENE
PIPE
• Wrap the thread of a 1¼" NPT x 1" male plastic pipe
adapter with PTFE tape if 1" pipe is being installed.
• Install the adapter into the pump discharge opening
while holding the discharge head with a pipe
wrench to prevent the head from loosening from the
pump housing.
• Install two 1" all stainless steel hose clamps over
one end of the pipe and tighten.
• Heat the polyethylene pipe to soften the pipe.
• Press the polyethylene pipe over the adapter.
• Tighten clamps securely around the pipe over the
adapter end.
• As the pump and pipe are lowered into the well,
the submersible wire cable must be secured to
the discharge pipe 5 feet from the top of the pump
using electrical tape or snap wire ties. Then repeat
this procedure at 10 foot (3 m) intervals along the
discharge piping.
INSTALLATION
Note: A pipe vise or collar clamp should always be firmly
affixed to the upper end of the pipe as it is being lowered.
• When the pump has reached the desired depth,
pass the pipe and cable through the openings in
the well seal. The discharge pipe goes through
the center hole and the cable through the conduit
opening. The well seal must be vented.
• Cut polyethylene pipe. Place two 1" clamps over
the end of the pipe.
• Heat the end of the pipe to soften the pipe.
• Install a 90 degree fitting at the top of the
discharge pipe.
Note: If the pipe was not cut, and the last section of
pipe has a female connector, use a 1" x 2" long nipple
and then thread the elbow into the nipple. Use PTFE
tape to seal joints.
• A 1" well seal elbow may be used instead of the 1"
male pipe thread adapter and elbow.
• Install the well seal into the well casing by tightening
down cap screws on the well seal. The well seal
must be vented.
• Continue pipe connection to the tank location in the
house. Continue securing the submersible pump
cable to the pipe. Additional clamps and fittings will
be required to make the necessary connections at
the elbow and at the control center.
INSTALLING THE PUMP WITH SEMI-RIGID
PLASTIC PIPE
• Wrap the thread of the pipe with PTFE tape.
• Thread the first section of the pipe into the pump
discharge opening.
• Sections are available in 10 and 20 foot lengths.
Use a pipe coupling and solvent to join pipe
sections together.
Note: A pipe vise or collar clamp should always be firmly
affixed to the upper end of the pipe as it is being lowered.
• As the pipe is lowered, the submersible wire cable
must be secured to the discharge pipe 5 feet from
the top of the pump using electrical tape. Then
repeat this procedure at 10 foot (3 m) intervals
along the discharge piping.
• When the pump has reached the desired depth,
pass the pipe and cable through the openings in
the well seal. The discharge pipe goes through
the center hole and the cable through the conduit
opening. The well seal must be vented.
• Cut the last section to the length required.
• Install a 1" or 1¼" male connector over the end of
the pipe using solvent to weld the pieces together.
• Wrap the threads of a 90 degree plastic elbow with
PTFE tape.
• Thread the elbow into the male connector.
Note: If the pipe was not cut, and the last section of
pipe has a female connector, use a 2" long nipple and
then thread the elbow into the nipple.
6
Loading ...
Loading ...
Loading ...