Loading ...
Loading ...
Loading ...
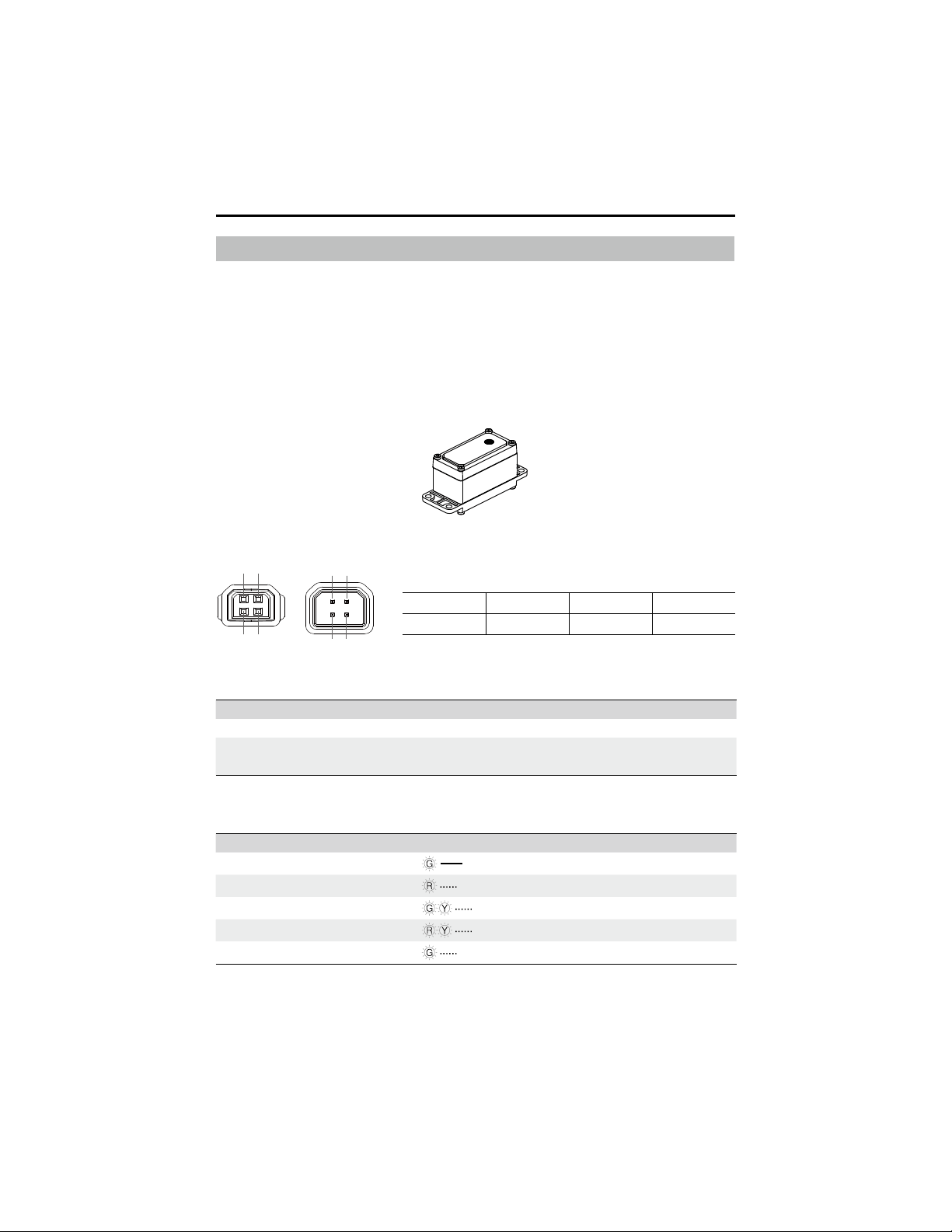
©
2020 DJI All Rights Reserved.
29
ROBOMASTER EP Core User Manual
Servo
Introduction
As a propulsion driver for the robot, the servo supports customized control abilities through the
programming interfaces of the robot. The servo ensures minimal gear backlash, high control
accuracy, and large output torque. Other uses include powering the robotic arm and supporting the
DC gear motor mode, which allows users to build lifting structures.
The servo uses RS485 bus mode and is compatible with PWM mode. When the servo is used
to drive the robotic arm, the system switches to RS485 bus mode automatically. When used
independently, the servo can operate in either RS485 bus mode or PWM mode. The system
automatically switches according to the input signal.
Servo PWM Port
The port pin is shown below:
The servo supports two control modes: angle mode and rate mode. The PWM signal has a
frequency of 50 Hz and a duty cycle ranging from 2.5% to 12.5%.
Control Mode Duty Cycle Control Range
Angle Mode 2.5% to 12.5% 0° to 360°
Rate Mode
2.5% to 7.5% 49 to 0 rpm
7.5% to 12.5% 0 to -49 rpm
LED Indicator Description for Servo
The LED indicator is used to indicate the status of the servo. Details are as follows:
LED Indicator Servo Status
Solid green
Working normally
Blinks red rapidly
Self-test error*
Blinks green and yellow alternatively
Overload protection**
Blinks red and yellow alternatively
Stalled***
Blinks green rapidly
The servo is selected in the RoboMaster app
* The servo will perform a self-test when it is powered on. If a self-test error occurs, reconnect the servo with the power supply.
Contact DJI Support if the servo still does not work normally after being powered on multiple times.
** The servo stops producing torque output after 200 milliseconds of overload, and automatically resumes output after three seconds.
*** If the servo stalls, check the current operation and reconnect the servo with the power supply.
1 2 3
4
485A/PWM 485B VCC-12V GND
1
4
2
3
2
3
1
4
Loading ...
Loading ...
Loading ...