Loading ...
Loading ...
Loading ...
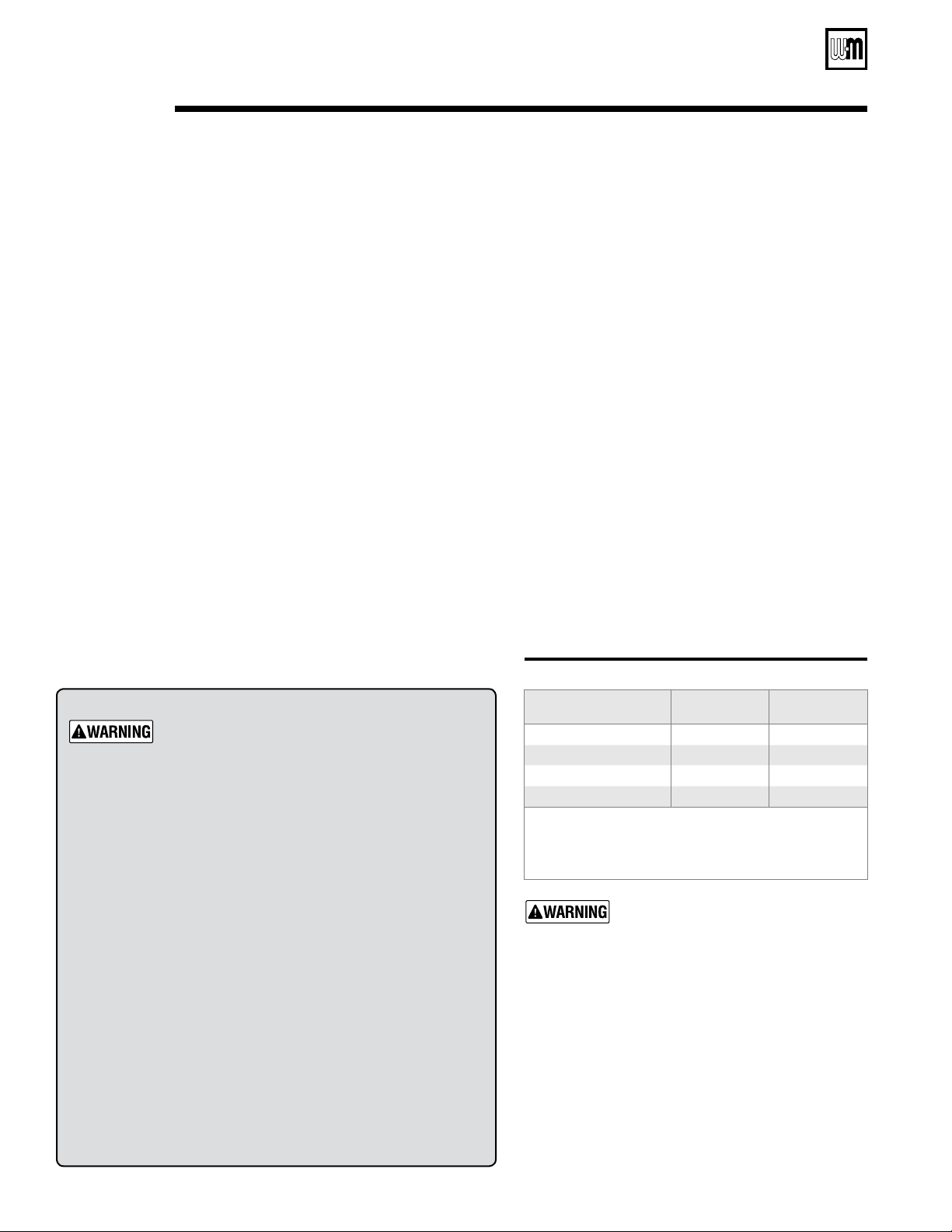
Part Number 550-142-300/0520
16
CGa Series 3 Gas-Fired Water Boiler — Boiler Manual
Water piping — general information
General piping information
If installation is to comply with ASME or Canadian requirements, an ad-
ditional high temperature limit is needed. Install control in supply piping
between boiler and isolation valve. Set second control to minimum 20°F
above setpoint of first control. Maximum allowable setpoint is 240°F.
See page 36, for wiring.
Use backflow check valve in cold water supply as required by local codes.
Water temperature/LWCO sensor
A low water cutoff device is required when boiler is installed above radia-
tion level or by certain state or local codes or insurance companies. The
boiler has a pre-installed water temperature/LWCO sensor.
Pressure/temperature gauge
Install pressure/temperature gauge in tee on supply piping (as shown in
drawing on page 3).
Isolation valves
Isolation valves are required to enable servicing of the boiler’s temperature
sensor. Install as shown in appropriate piping diagram.
Relief valve
Install relief valve vertically in ¾” tapping on side of boiler. See Figure 9
or 10
, page 17, and the tag attached to the relief valve for manufacturer’s
instructions.
Chillers or air handling units:
Install boiler such that —
• Chilled medium, if used, is piped in parallel with
heating boiler. Use appropriate valves to prevent
chilled medium from entering boiler. Consult AHRI
Installation and Piping Guides.
• If boiler is connected to heating coils located in
air handling units where they can be exposed to
refrigerated air, use flow control valves or other
automatic means to prevent gravity circulation
during cooling cycle. Circulation of cold water
through the boiler could result in damage to the heat
exchanger, causing possible severe personal injury,
death or substantial property damage.
Circulator
The circulator is shipped loose (wiring pre-attached to
boiler) to allow you to locate it either in the return or
supply piping, as desired. See page 3 for a typical instal-
lation. Pipe the expansion tank to the suction side of the
circulator whenever possible. Install an air separator in
the supply piping. Connect the expansion tank to the air
separator only if the separator is on the suction side of
the circulator. Always install the system fill connection
at the same point as the expansion tank connection to
the system. Figures 9 and 10 show typical near-boiler
piping connections.
System water piping
See Figure 9 (diaphragm-type or bladder-type expansion
tank) or Figure 10 (closed-type expansion tank), and
Table 3 below, for near-boiler and single-zone systems
designed for return water at least 130°F.
See pages 18-19 to complete multiple-zone piping or
pages 20-25 to complete piping for radiant heating sys-
tems or converted gravity systems (large-volume systems
originally designed for circulation by natural convection
rather than a pump). See page 25 for boilers used with
refrigeration systems.
To avoid water damage or scalding due to relief
valve operation:
• Discharge line must be connected to relief valve outlet and run to a
safe place of disposal
. Terminate the discharge line to eliminate
possibility of severe burns should the valve discharge.
• Discharge line must be as short as possible and be the same size
as the valve discharge connection
throughout its entire length.
• Discharge line must pitch downward from the valve and terminate
at least 6” above the floor drain where any discharge will be clearly
visible.
• The discharge line shall terminate plain, not threaded, with a
material serviceable for temperatures of 375°F or greater.
• Do not pipe the discharge to any place where freezing could
occur.
• No shutoff valve shall be installed between the relief valve and
boiler, or in the discharge line. Do not plug or place any obstruc-
tion in the discharge line.
• Failure to comply with the above guidelines could result in fail-
ure of the relief valve to operate, resulting in possibility of severe
personal injury, death or substantial property damage.
• Test the operation of the valve after filling and pressurizing
system by lifting the lever. Make sure the valve discharges freely.
If the valve fails to operate correctly, replace it with a new relief
valve.
Table 3 Water pipe size (based on 20°F rise)
Boiler model To
system
From
system
CGa-25
¾” ¾”
CGa-3, 4, 5
1” 1”
CGa-6, 7
1¼” 1¼”
CGa-8
1½” 1½”
Note: The boiler supply and return connections, the return/
drain tee and the supply/gauge tee supplied with
the boiler are 1¼” NPT. One of the circulator flanges
supplied with the boiler is 1¼”. The other circulator
flange is the size of the recommended system piping
shown above.
3a
Loading ...
Loading ...
Loading ...