Loading ...
Loading ...
Loading ...
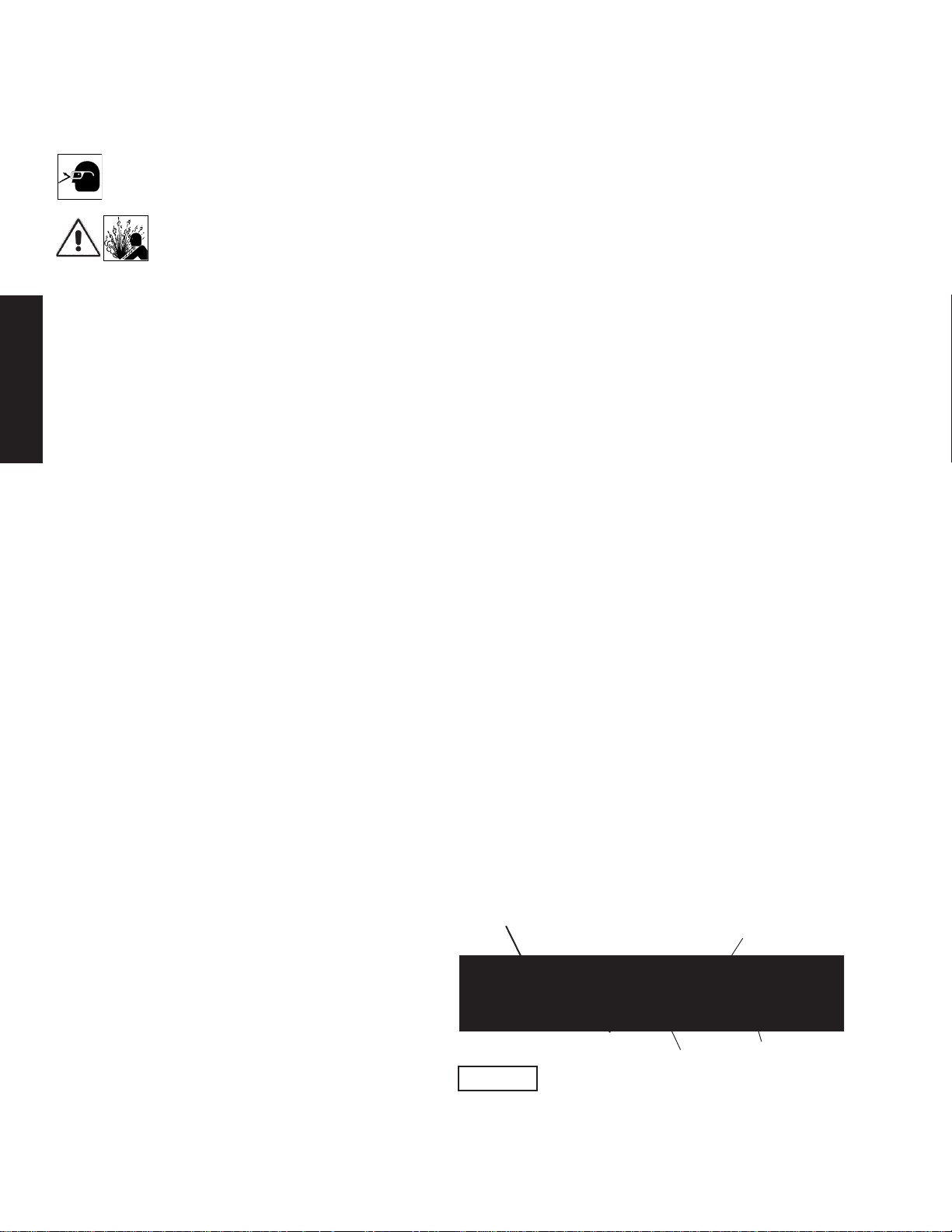
8
E
N
G
L
I
S
H
If,
after ! ve minutes, the pressure is still holding constant, and
no “bubbles” are observed, slowly bleed the pressure and
remove the gauge assembly. Replace the pipe plug using a
sealant. If the pressure does not hold, then the leak must be
located. If no leaks are detected !
ll with oil per F-1.3.
CAUTION: - Always wear eye protection when
working on pumps.
CAUTION: - Pressure builds up extremely
fast; increase pressure by “TAPPING” air
nozzle. Too much pressure will damage
seal. DO NOT exceed 6 P.S.I.
F-2) Impeller and Volute Service:
F-2.1) Disassembly and Inspection:
Disconnect discharge piping. Remove cap screws (16) and
pull volute (1) and gasket (32) from the intermediate (5).
Examine volute and gasket, replace if required. Remove set
screw (39). The impeller (2) is screwed onto the motor shaft,
and to loosen turn counter clockwise. Examine the impeller
for pitting or wear and replace if required.
F-2.2) Reassembly:
At reassembly, make sure that the shims (3) are in place
to ensure proper clearance between the impeller (2) and
intermediate (5). Clearance should be approximately .03
inches. Screw impeller (2) onto motor shaft in the clockwise
direction, screw in set screw (39) and tighten. Place gasket
(32) and volute (1) onto intermediate (5) and insert cap
screws (16) and tighten.
F-3) Strainer:
F-3.1) Disassembly and Inspection:
The screen (7) should be periodically cleaned. This is
accomplished by simply removing the springs (24) and lifting
off the screen.
F-3.2) Reassembly:
Slide screen (7) back on, lining up between pump supports
(25) and reattach springs (24).
F-4) Diaphragm, Shaft Seal & Motor:
F-4.1) Disassembly and Inspection:
Remove volute and impeller as outlined in paragraph F-2.1.
Remove screen as outlined in paragraph F-3.1. Remove pipe
plug (38) and drain the oil from the pump. Loosen gland nut
(13) and slide it back on the cord set (14). Remove hex nuts
(22) and lock washers (23) from studs (28) and pull housing
end piece (21) from the housing tube (27). Be careful not
to damage diaphragm (15) when removing housing end
piece (21). Disconnect cord set (14) and check for cracks or
damage and replace if required. To check or replace grommet
(11), remove friction rings (12) from end piece (21) and
remove grommet (11), see FIGURE 6.
To replace diaphragm (15) remove cap screws (16) and plate
(42) from Housing end piece (21). Remove diaphragm (15),
back up ring (20), spring (19), spring guide (17) and screen
(18) from housing end piece (21). Pull Housing tube (27) from
intermediate (5). Remove seal spacer (40) and v-ring (41)
from shaft. Loosen motor screws and pull the intermediate (5)
with the shaft seal (30) from the motor (6).
NOTE: Mark location of overload in relation to intermediate
(5). Remove retaining ring (4) and press seal assembly (30)
out of the intermediate (5). Examine seal for signs of wear
such as uneven wear pattern on stationary members, chips
and scratches on either seal face. DO NOT interchange seal
components, replace entire seal if any part shows wear or
damage.
Examine o-rings (26), replace if cut or damaged. Inspect
motor windings for shorts and check resistance values.
Check rotor for wear, if rotor or the stator windings are
defective, the complete motor must be replaced. To test
the Overload, check the continuity between the black and
white wires. If found to be defective contact a motor service
station or Barnes Pump’s Service Department. Check motor
capacitor (9) and replace if defective.
F-4.2) Reassembly:
Assemble intermediate (5) onto the motor (6), locating
overload as noted above (or at the 11 o’clock position as
viewed from the motor end), with the four motor bolts, with
capacitor bracket (31) on one of the bolts.
Place one o-ring (26) into groove on intermediate (5) and
being careful not to cut or damage o-ring (26) slide housing
tube (27) onto intermediate (5). Reassemble housing end
piece (21) by ! rst placing screen (18) into end piece (21).
Place spring guide (17) and spring (19) over projection on
diaphragm (15). Insert back-up ring (20) into diaphragm (15)
making sure lip of diaphragm (15) is in the groove of back-up
ring (20). Now assemble diaphragm assembly to housing end
piece (21) with plate (42) and cap screws (16). Slide capacitor
(9) into bracket (31) and connect fl ag terminals from motor
and terminal boot (8) to capacitor (9). Place o-ring (26) into
groove on housing end piece (21) and slide end piece (21)
into housing tube (27) being careful not to cut or damage
o-ring (26). Place pump support (25) onto the lower studs (28)
and place lock washers (23) and hex nuts (22) onto studs (28)
and tighten.
Insert seal retaining ring (30a) along with spring (30b) onto
motor shaft until seated. Lightly oil motor’s shaft (DO NOT
use grease) and inner surface of rotating member (30c) and
seal assembly bullet (see parts list-Seal Tool Kit). Place the
bullet over shaft threads and with lapped surface facing out,
press rotating member (30c) with a Seal Pusher (see parts
list- Seal Tool Kit) onto shaft and into intermediate assembly
(5) until it seats against shoulder on shaft see FIGURE 3.
FIGURE 3
Rotating Member (30c)
Bullet
Motor (6) &
Intermediate (5)
Seal Pusher
Retaining Ring (30a)
Spring (30b)
Loading ...
Loading ...
Loading ...