Loading ...
Loading ...
Loading ...
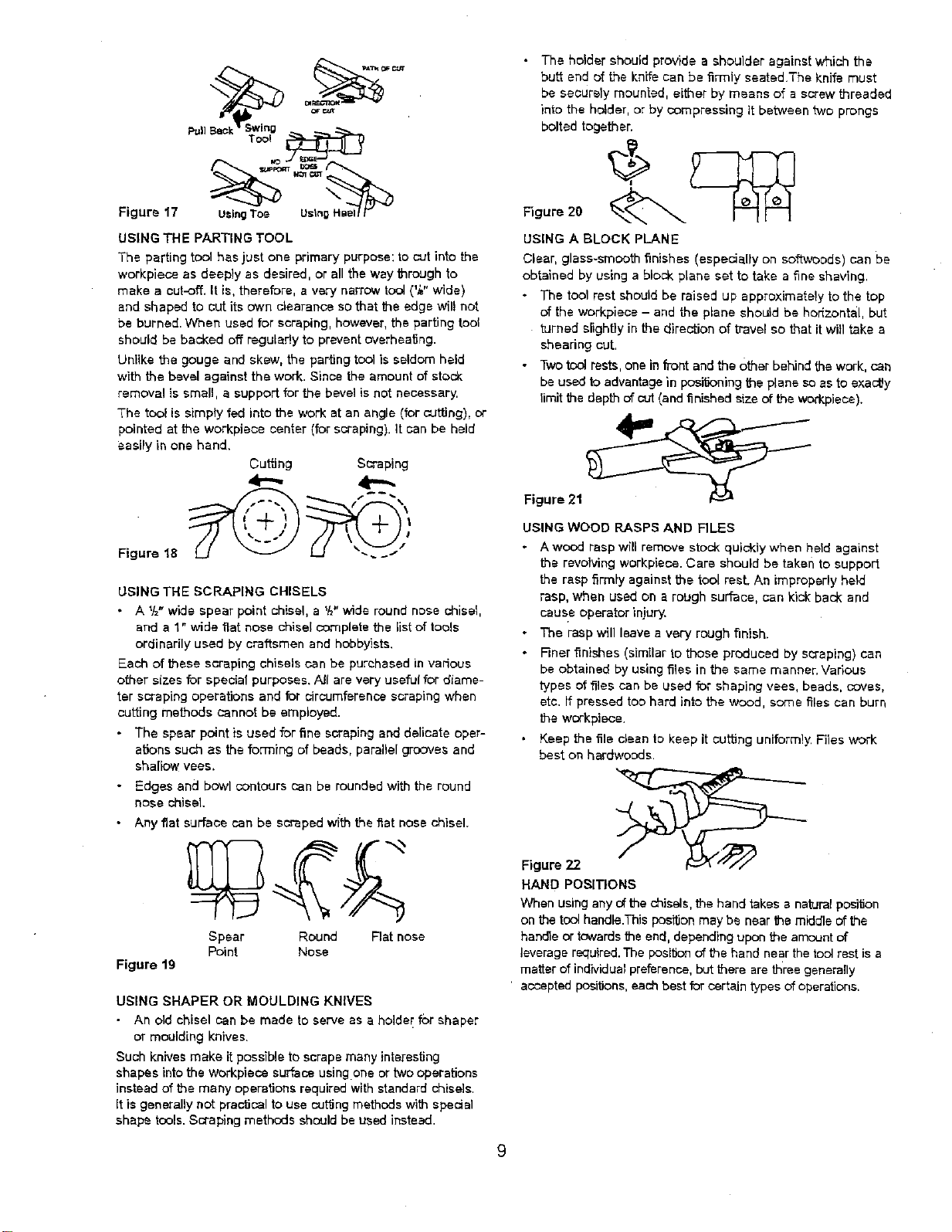
Figure 17
USING THE PARTING TOOL
The parting fool has just one primary purpose: to cut into the
workplace as deeply as desired, or all the way through to
make a cut-off. It is, therefore, a very narrow tool ('6" wide)
and shaped to cut its own clearance so that be edge wil! not
be burned. When used for scraping, however, the parting tool
should be backed off regularly to prevent overheating.
Unlike the gouge and skew, the parfing tcol is seldom held
with the bowl against the work. Since the amount of stock
removal is small, a support for the bevel isnot necessary
The tool is simply fed into the work at an angle (for cutting), or
pointed at the workpiece center (for scraping). It can be held
easily in one hand.
Cutting Scraping
4--,,
USING THE SCRAPING CHISELS
• A I/Z wide spear point chisel, a _h"wide round nose chisef,
and a 1" wide fiat nose chisel complete the list of tools
ordinarily used by craftsmen and hobbyists.
Each of these scraping chisels can be purchased invarious
other sizes for special purposes. AJfare very usefof for diame-
ter scraping operations and for circumference scraping when
cutting methods cannot be employed.
• The spear point is used for fine scraping and delicate oper-
ations such as the forming of beads, parallel gram/as and
shallow yeas.
• Edges and bowl contours can be rounded with the round
nose chisel.
Any fiat surface can be scraped with the fiat nose chisel.
Spear Round Fiat nose
Point Nose
Figure lg
USING SHAPER OR MOULDING KNIVES
An old chisel can be made to serve as a holder for shaper
or moulding knives.
Such knives make it possible to scrape many interesting
shapes intothe workpiece surface using one or two operations
instead of the many operations required with standard chisels.
It isgenerally not practical to use cut_ng methods with special
shape tools.Scraping methods should be used instead.
• The holder should pray'tales shoulder against which the
butt end of the knife can be firmly seated.The knife must
be securely mounted, either by means of a screw threaded
into the ho_der, or by compressing it between two prongs
bolted together.
Figure 20 _ _
USING A BLOCK PLANE
Clear, glass-smooth finishes (especially on softwoods) can be
obtained by using a block plane set to take a fine shaving.
• The tool rest should be raised up approximately to the top
of the workplace - and the plane should be horlzontal, but
turned slightly in the direction of travel so that it will take s
shearing cut,
• Two tool rests, one in frontand the other behind the work, can
be used to advantage in positioning the plane so as to exactly
1imitthe depth of cut (and finished size of the work.piece).
Figure 21
USING WOOD RASPS AND FILES
• A wood rasp will remove stock quickly when held against
the revolving wcrkpiece. Care should be taken to support
the rasp firmly against the tool rest. An improperly held
rasp, when used on a rough surface, can kick back and
cause operator injury.
• The rasp will leave a very rough finish.
• Finer finishes (similar to those produced by scraping) can
be obtained by using files in the same manner. Various
types of files can be used for shaping vees, beads, coves,
etc. If pressed too hard into the wood, soma files can burn
the workplace.
Keep the file clean to keep it cutting uniformly, Files work
best on hardwoods.
Figure 22
HAND POSITIONS
When using any of the chisels, the hand takesa natural position
on the tool handle.This pos_on may be near the middle of the
handle or towards the end, depending upon the amount of
leverage required.The position of the hand near the tool rest is a
matter of individual preference, but there arethree generally
accepted positions, each best for certain types of operations.
9
Loading ...
Loading ...
Loading ...