Loading ...
Loading ...
Loading ...
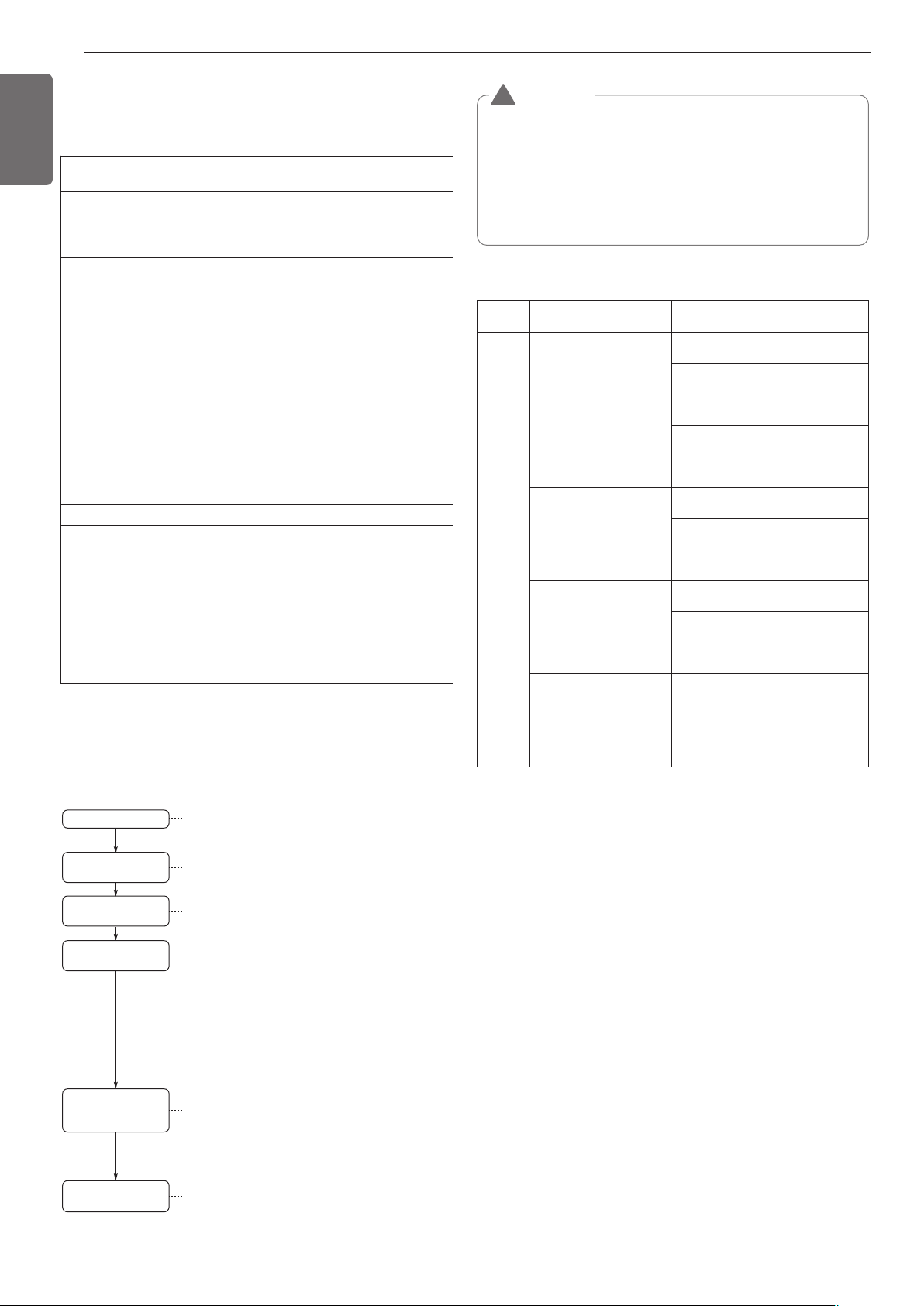
38
ENGLISH
WARNING
• Always check whether the water supply is flowing smoothly
before the test run. (If sufficient amount of water is not flow-
ing, it can burn the product.)
• During the initial test run after installing the product, leaving
the product for more than 3 days or after replacing the com-
pressor, power must be connected 6 hours prior to the opera-
tion to heat the compressor heater. (If the product is not
heated sufficiently, it can burn the product.)
!
How to Cope with Abnormal Test Run
Maintenance of plate type heat exchanger
Item
Phenom-
enon
Cause Checkpoint and resolution
Whether
heat
water is
supplied
CH24
When connecting
the flow switch,
heat-sourced
water doesn’t
flow or the
amount of its flow
lacks due to the
checked error re-
lated to heat-
sourced water.
Check whether the heat source water
supply pump is operating.
Check whether the heat source water
supply pipe is clogged.
(Clean strainer, valve locked, valve
issue, air trapped etc.)
Check whether the flow switch is nor-
mal condition.
(Flow switch problem, arbitrary con-
trol, disconnection etc.)
CH32
Heat water not
supplied or flow
rate is insufficient
Check whether heat source water
supply pump is operating.
Check whether the heat source water
supply pipe is clogged.
(Clean strainer, valve locked, valve
issue, air trapped etc.)
CH34
Heat water not
supplied or flow
rate is insuffi-
cient(During Cool-
ing)
Check whether heat source water
supply pump is operating.
Check whether the heat source water
supply pipe is clogged.
(Clean strainer, valve locked, valve
issue, air trapped etc.)
CH180
Heat water not
supplied or flow
rate is insufficient
(During heating)
Check whether heat source water
supply pump is operating.
Check whether the heat source water
supply pipe is clogged.
(Clean strainer, valve locked, valve
issue, air trapped etc.)
❈ When CH24 or CH180 error occurs during the test operation of the
heater, the inside of the panel heat exchanger may be partially
frozen and therefore, be sure to get rid of its cause and then, re-op-
erate the device.
(The root cause of partial freezing: The lack of flow of heat-sourced
water, suspension of water, lack of cooling medium, infiltration of
foreign substance inside of panel heat exchanger )
Water supply system test run
Before executing the test run for the product, you must first test the
heat source water system.
The test run for the product must be executed after checking the flow
rate and temperature of the heat source water supplied.
Equipment design
Execute the
product test run
Water pipe system
installation
Water supply pipe
and product connection
Water supply
system test run
Judging whether there
is any problem with
the water supply
Design the system including cooling tower, boiler, pump etc.
- Check the equipment capacity (Water volume, temperature
control range).
Connect the water pipe to the inlet/outlet of the product so
that the water can be supplied to the product.
Execute water supply system test run
- The product does not operate but the pump and water
supply equipment will operate to flow the Heat source
water to the heat exchanger on the product side.
- Flow the water to all water piping system to clean any alien
particles inside the pipes and execute an air purge to
remove an air within the pipes to make the water supply
smoother.
- Clean all the strainers of water pipe including around
outside units.
Execute the test of water supply system without operating
the product.
- Check whether outside unit inlet/outlet flow rate complies
to the product specification. Standard Water volume is
96LPM based on 10HP and 196LPM based on 20HP.
- Check the water supply temperature. whether is OK
After checking the normal condition of the water supply,
execute the test run of the product.
To prevent the freezing of the heat exchanger when the
refrigerant is discharged with the water supply blocked,
discharge the refrigerant after draining out around the
outside unit.
Install the water pipe
1
Check whether the air is completely removed and the water sup-
ply is flowing smoothly.
2
Check whether there is any refrigerant leakage of any disconnected
or loose communication or power wire, or use the electric wiring dia-
gram to check the wiring connection condition. Check whether the
power and communication wire are connected.
3
Check whether the power cable R, S, T and N are correctly con-
nected. Check the insulation resistance with the DB mega tester
device (DC 500V) between the power terminal block and ground-
ing, and check whether it is 2.0MΩ or above when measured.
If the resistance is 2.0MΩ or less, do not operate the product.
Precaution)
- Never check the insulation resistance for the terminal control
board. (The control board can be damaged.)
-
If you leave the system turned off right after the installation or for a
long period of time, the refrigerant gets accumulated within the
compressor and the insulation resistance reduces to less than 2
MΩ. When the insulation resistance is 2 MΩ or less, turn on the
power and let the electricity be supplied to the crank case heater of
the compressor and let the refrigerant including the oil inside the
compressor to evaporate. Then the insulation resistance value will
increase to more than 2.0 MΩ.
4 Check whether the liquid and gas pipes are open.
5
Precaution when blocking the water cooling type Multi V main power
- While using the product (Air conditioning season/Heating season), al-
ways connect the main power of the outside unit.
-
During the test run operation after installing the product or during the oper-
ation after blocking the outside unit main power (Power outage etc.), you
must always connect the power 6 hours prior to heating the crank case
heater. If the crank case is not preheated for more than 6 hours with the
electric heater, it can cause a burn on the compressor.
(Heating the bottom part of the compressor with the crank case heater is
to evaporate the refrigerant included in the oil inside the compressor.)
As the scales are created in the panel heat exchanger, its efficiency
may decrease or damage may occur due to winter-sowing due to the
decrease in its flow.
Due to this reason, regular maintenance is necessary so that the scales
shouldn't be created.
1 Before the season of use, check below points.(Once a year)
1) Inspection on water quality to check if this is within the standard
condition.
2) Clean the strainer.
3) Check if the flow is appropriate.
4) Check if the operation environment is appropriate.(Pressure,
flow, output temperature)
2 Below procedure should be abided by in order to clean the panel
heat exchanger. (Once every 5 years)
1) Check if the service port is equipped with the water pipe in order
to clean the chemical solution.
5% diluted formic acid, citric acid, oxalic acid, acetate acid, phos-
phoric acid and etc. are appropriate for the chemical solution for
wiping out the scales.(Hydrochloric acid, sulphuric acid, nitric acid
and etc. shouldn't be used due to its corrosion.)
TEST RUN
Precaution before test run
Loading ...
Loading ...
Loading ...