Loading ...
Loading ...
Loading ...
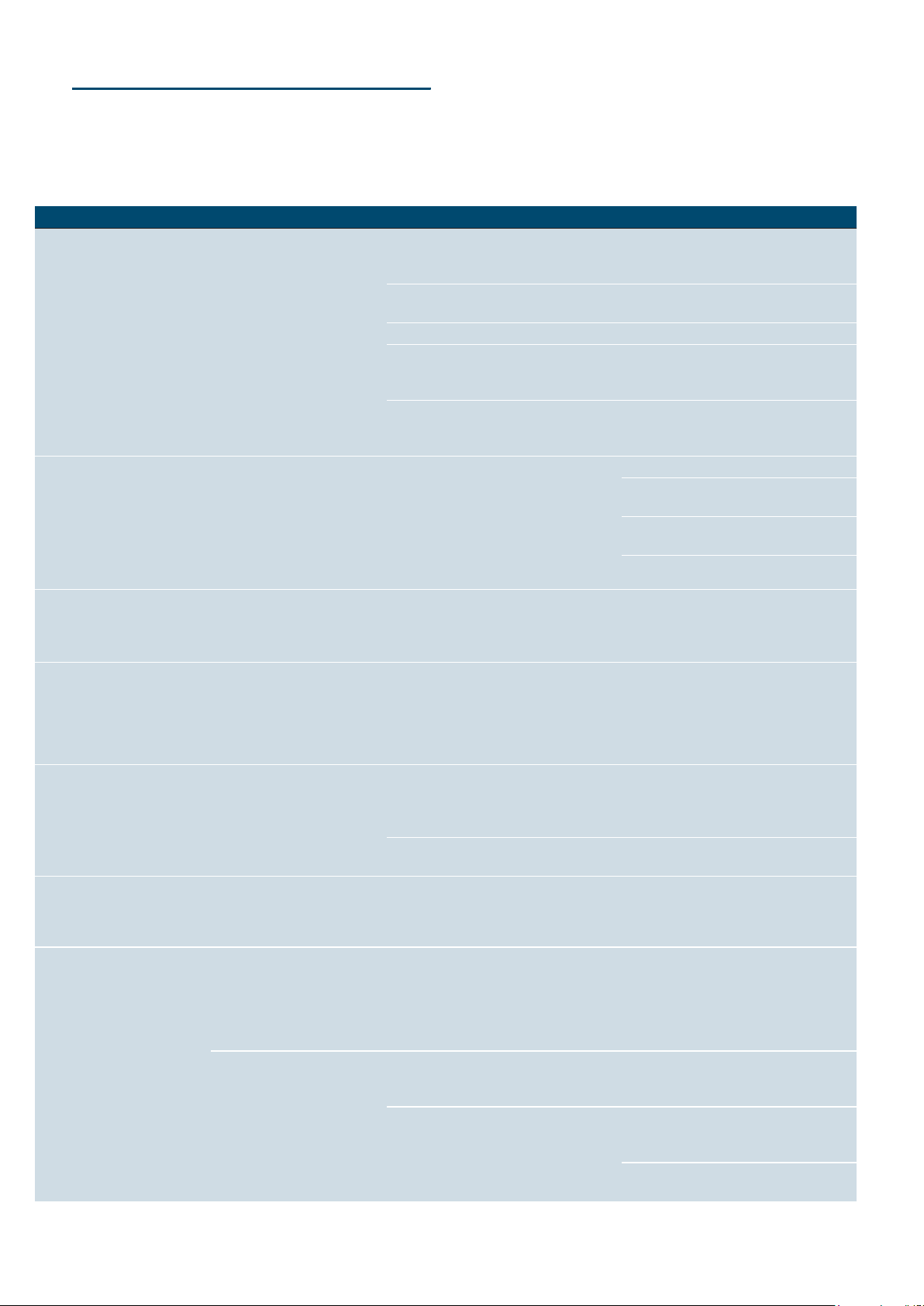
en Cleaning
12
DCleaning
Cl eani ng
Only clean the appliance when it has been switched off.
Ensure that the sealing bar in the vacuuming chamber
has cooled down.
:Warning – Risk of burns!
The sealing bar in the vacuuming chamber becomes
extremely hot if the appliance is used frequently and
there are long heat-sealing times. Never touch the hot
sealing bar. Keep children away from the appliance.
During cleaning, ensure that no water or other liquid
gets into the vacuum-sealing compartment or, in
particular, into the vacuum pump's air outlet. Never
spray the inside or outside of the appliance with water.
Do not use a high-pressure cleaner or steam jet
cleaner.
Only use natural cleaning agents, such as washing-up
liquid and water. Do not use any abrasive materials or
cleaning agents that contain alcohol.
Clean the appliance using only a damp cloth.
Do not use any abrasive sponges that may scratch or
any glass scrapers.
Note: Leave the appliance and accessory parts to fully
dry after they have been cleaned.
Glass front and glass lid
Clean the glass front and the glass lid with glass
cleaner and a soft cloth.
Do not use any abrasive sponges that may scratch or
any glass scrapers.
Stainless steel vacuuming chamber
Always remove flecks of limescale, grease, starch and
albumin (e.g. egg white) immediately. Corrosion can
form under these patches or splashes. Clean with water
and some washing-up liquid. Dry the surface with a soft
cloth.
Plastic control panel
Do not use any abrasive sponges that may scratch or
any glass scrapers.
Sealing bar
Remove the remaining film from the sealing bar.
Never use abrasive cleaning agents to clean the sealing
bar. Use a soft cloth.
The sealing baris not suitable for dishwashers.
External vacuum-sealing adapter
Wash the adapter by hand. It is not suitable for
dishwashers.
Vacuum hose
Rinse the vacuum hose by hand. It is not suitable for
dishwashers.
Trouble shooting en
13
3Trouble shooting
Tr oubl e shoot i ng
Faults often have simple explanations. Before you call
our after-sales service, please read the information in
the table below.
Note: Any repair work must only be carried out by
qualified experts. Incorrect repairs to your appliance
may present considerable risks for the user.
Fault Error Causes Possible remedy
The : symbol will appear
after a few seconds.
The vacuum cannot be cre-
ated properly.
The glass lid has not been closed prop-
erly.
Open and close the glass lid again.
When doing so, lightly press on the glass
lid for the first few seconds.
The seal on the glass lid is not fitted
properly or is defective.
Check the seal.
The seal on the glass lid has deformed. Gently press the seal to straighten it out.
The lid on the external vacuum-sealing
container has not been closed properly.
Check the position of the vacuum-seal-
ing lid. Only use suitable vacuum-sealing
containers.
The external vacuum-sealing connection
is not positioned correctly on the vac-
uum-sealing chamber's air outlet.
Check the position of the external vac-
uum-sealing connection.
The : symbol will appear
after the pump has been run-
ning for 2 minutes.
It is taking too long to create a
vacuum. Your selected vac-
uum-sealing level cannot be
reached.
As the temperature rises, liquids begin to
boil. At this point, the process of creating
a vacuum stops.
Only vacuum-seal cold liquids.
If the vacuum-sealing chamber is wet,
wipe it dry.
Heat-seal the vacuum-sealing bag early if
large bubbles form.
Select a lower vacuum-sealing level.
The vacuum-sealing process
will not start. The
Start symbol does not appear
even though the lid is closed.
The appliance is not detecting
the lid.
The door switch on the glass lid is miss-
ing or is not being detected by the appli-
ance.
Call the after-sales service.
If you try to operate the appli-
ance several times in succes-
sion, the vacuum-sealing
process seems to run as nor-
mal but the bag is not heat-
sealed.
The thermal switch on the heat-sealing
transformer has been triggered.
Allow the appliance to cool for at least
10 minutes. Then try again.
Allow the appliance to cool for at least
2 minutes between vacuum-sealing
operations.
The vacuum-sealing process
is taking longer and longer.
There is too much moisture in the pump
system.
The appliance monitors the vacuum-
sealing as it progresses. If too much liq-
uid is retained in the pump oil, the
¢ symbol will appear. Initiate drying.
The pump system is extremely hot. Allow the appliance to cool and then try
again.
After the drying cycle has
ended, the appliance is dis-
playing the ¢ and :
symbols.
One drying cycle alone was not suffi-
cient.
Wait until the : symbol is no longer lit
up. Then start another drying cycle.
The vacuum in the plastic bag
is not retained.
The bag is defective. Sharp parts of the food (for example
bones) may poke holes in the bag.
Check the bag for damage. Use a differ-
ent bag if it is damaged. If the damage is
caused by sharp-edged parts of the food,
as far as possible, position these in the
bag in such a way that they cannot dam-
age the wall of the bag.
The heat-sealed seam is
defective.
The heat-sealing time you have selected
is unsuitable for the plastic from which
the bag is made.
Select a different heat-sealing time.
There is liquid, grease or crumbs along
the heat-sealed seam. The bag has
creases along the heat-sealed seam.
Make sure that the bag is dry, that it has
no creases, and that it is positioned fully
on the heat-sealing bar.
Use a different bag. Fold over the edge
of the bag by 3 cm before you fill it.
Loading ...
Loading ...
Loading ...