Loading ...
Loading ...
Loading ...
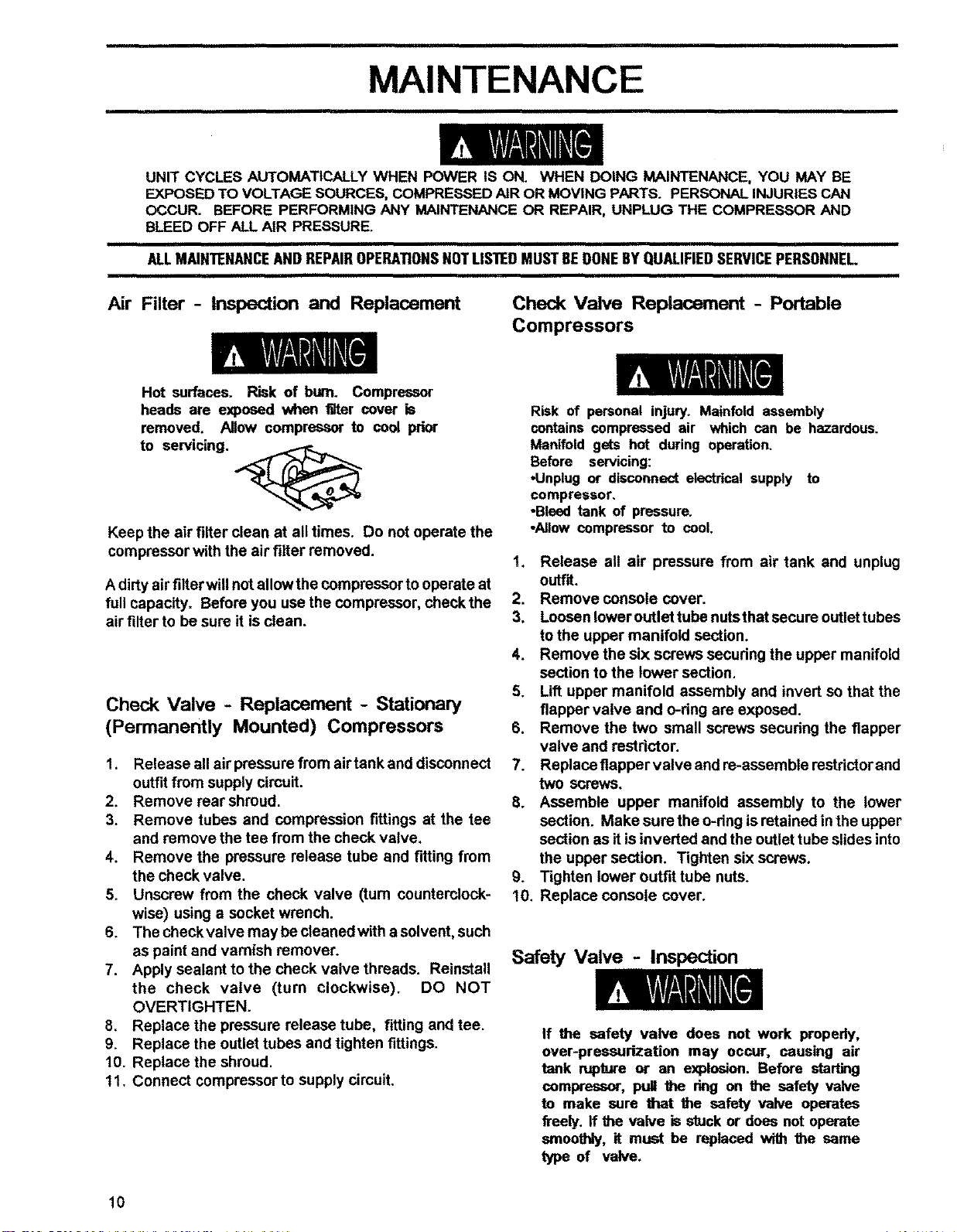
MAINTENANCE
iiiii
UNIT CYCLES AUTOMATICALLY WHEN POWER IS ON. WHEN DOING MAINTENANCE, YOU MAY BE
EXPOSED TO VOLTAGE SOURCES, COMPRESSED AIR OR MOVING PARTS. PERSONAL INJURIES CAN
OCCUR. BEFORE PERFORMING ANY MAINTENANCE OR REPAIR, UNPLUG THE COMPRESSOR AND
BLEED OFF ALL AIR PRESSURE.
ALLMAINTENANCEAND REPAIROPERATIONSNOTLISTEDMUSTBEDONEBYQUALIFIEDSERVICEPERSONNEL.
Air Filter - Inspection and Replacement Check Valve Replacement - Portable
Compressors
Risk of burn.
Hot surfaces. Compressor
heads are exposed when filter cover is
removed. Allow compressor to cool prior
to servicing. _
Keep the air filter clean at all times. Do not operate the
compressor with the air filter removed.
A dirty air filter will not allowthe compressor tooperate at
full capacity. Before you use the compressor, check the
air filter to be sure it is clean.
Check Valve - Replacement - Stationary
(Permanently Mounted) Compressors
1. Release all air pressure frcm air tank and disconnect
outfitfrom supply circuit.
2. Remove rear shroud.
3. Remove tubes and compression fittings at the tee
and remove the tee from the check valve.
4. Remove the pressure release tube and fitting from
the check valve.
5. Unscrew from the check valve (turn counterclock-
wise) using a socket wrench.
6. The check valve may be cleaned with a solvent, such
as paint and varnish remover.
7. Apply sealant to the check valve threads. Reinstall
the check valve (turn clockwise). DO NOT
OVERTIGHTEN.
8. Replace the pressure release tube, fitting and tee.
9. Replace the outlet tubes and tighten fittings.
10, Replace the shroud.
11. Connect compressor to supply circuit,
Risk of personal injury. Mainfold assembly
contains compressed air which can be hxTardous.
Manifold gets hot during operation.
Before servicing:
•Unplug or disconnect electdcel supply to
compressor.
-Bleed tank of pressure.
•Allow compressor to cool.
t. Release all air pressure from air tank and unplug
outfit.
2. Remove console cover.
3. Loosen lower ouUettube nutsthat secure outtettubes
to the upper manifold section.
4. Remove the six screws secudng the upper manifold
section to the lower section.
5. Lift upper manifold assembly and invert so that the
flapper valve and o-dng are exposed.
6. Remove the two small screws secudng the flapper
valve and restdctor.
7. Replace flapper valve and re-assemble restdctorand
two screws.
8. Assemble upper manifold assembly to the lower
section. Make sure the o-dng is retained in the upper
section as itis inverted and the outlet tube slides into
the upper section. Tighten six screws.
9. Tighten lower outfit tube nuts.
10. Replace console cover.
Safety Valve - Inspection
If the safety valve does not work properly,
over-pressurization may occur, causing air
tank rupture or an explosion. Before starting
compressor, pull the ring on the safety valve
to make sure that the safety valve operates
fTeely.If the valve is stuck or does not operate
smoothly, it must be replaced with the same
type of valve.
10
Loading ...
Loading ...
Loading ...