Loading ...
Loading ...
Loading ...
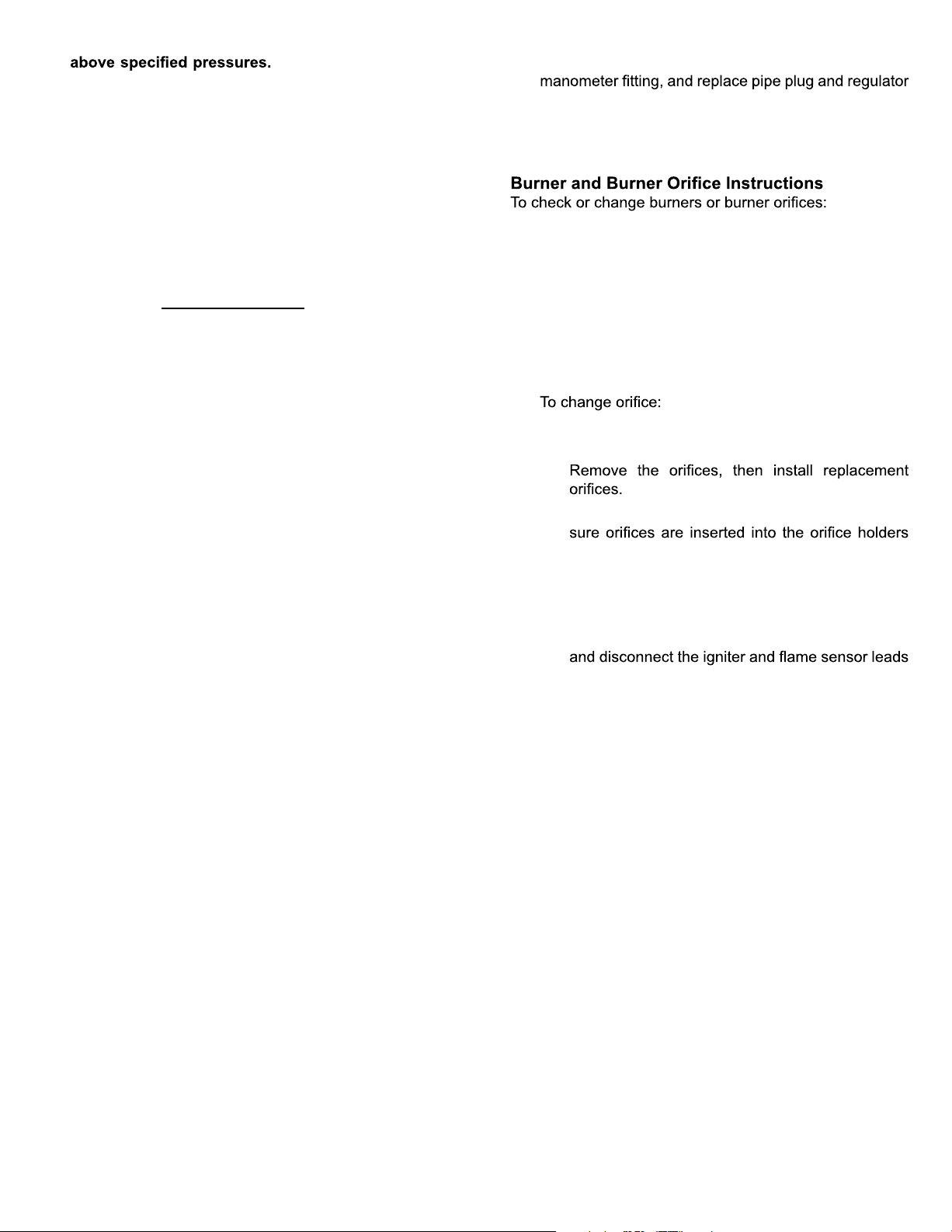
507295-02C Page 9 of 13mrcool.com
To adjust the regulator, turn
the adjusting screw on the regulator clockwise to increase
pressure and input or counterclockwise to decrease
pressure and input. See Figure 7 to assist in locating the
regulator on the gas valve.
Check the furnace rate by observing the gas meter, making
sure all other gas appliances are turned off. The test hand
on the meter should be timed for at least one revolution,
noting the number of seconds per revolution. The heating
value of the gas can be obtained from the local utility.
BTU/HR
Input
=
Cubic Feet per
Revolution
x 3600 x
Heating
Value
# Seconds per
Revolution
For example, by actual measurement, it takes 38 seconds
for the hand on the 1-cubic foot dial to make a revolution
with a 100,000 BTU/HR furnace running. The result is
99,750 BTU/HR, which is close to the 100,000 BTU/HR
rating of the furnace.
Manifold Gas Pressure Adjustment Regulator – LPG/
Propane Gas
LPG/propane units require a LPG regulator on both the
gas valve and on the LPG/propane tank.
IMPORTANT: For purpose of input adjustment, the
minimum permissible gas supply pressure (inlet side of
gas valve) is 11” w.c. for LPG/propane.
If at any time ignition is slow and burner does not seem to
be operating correctly, check manifold pressure (outlet side
of the gas valve). It should be 10” to 10.5” w.c. pressure
for LPG/propane.
The furnace is designed to obtain rated input at 10”
w.c. manifold pressure for propane.
High Altitude
The input rate shown on the rating plate is for elevations
up to 2000 feet. For elevations from 2001 to 4500 feet,
the input rate is reduced by 5%. For elevations above
4500 feet, refer to the National Fuel Gas Code Z223.1
(latest edition) or the Canadian Installation Codes CAN/
CGA-B149.1 & B149.2 for further details.
To check this pressure:
1. Slide the gas valve switch to the “OFF” position (see
Figure 7).
2. Remove plug on valve marked “OUTLET PRESSURE.”
3. Install a water manometer.
4. Slide the gas valve switch to the “ON” position and
initiate a call for heat.
If manifold pressure must be
adjusted, remove cap from pressure regulator and
turn adjustment screw clockwise to increase pressure
or counterclockwise to reduce pressure.
5. After checking pressure, turn gas off, remove
cap.
6. Put furnace in operation and check plug for leaks
using soapy solution.
1. Close the main manual gas shutoff valve and turn
off all power to unit.
2. Remove the burner access panel.
3. Disconnect the union in the gas supply line upstream
of the gas valve and downstream of the manual shutoff
valve.
4. Label wires going to the gas valve, then disconnect
the wires.
5.
a. Remove screws that fasten the manifold to the
burner box assembly and remove the manifold.
b.
c. To reassemble: Reverse above steps, making
on the back end of the burners, and that burners
are level and centered on each burner opening in
the vest panel.
6. To remove or service burners:
a. Label and disconnect the wires to the rollout switch
at the ignition control.
b. Remove the screws that secure the burner box
assembly to the vest panel and remove the
assembly from the unit.
c. Remove the screws that fasten the burner rack
and bottom shield assembly to the burner box.
Burners are now accessible for removal.
d. To Reassemble: Reverse above steps.
7. After reassembly of all parts is complete and all wires
are reconnected, open the main manual gas shutoff
valve; check for and correct any gas leaks. Turn
electrical power on, initiate a call for heat, and check
for proper burner operation.
8. Install burner access panel.
Heat Anticipator
The heat anticipator setting is 0.75 amp. It is important
that the anticipator setpoint be correct. Too high of a setting
will result in longer heat cycles and a greater temperature
swing in the conditioned space. Reducing the value below
the correct setpoint will give shorter “ON” cycles and
may result in the lowering of the temperature within the
conditioned space.
Loading ...
Loading ...
Loading ...