Documents: Go to download!
User Manual
- Owner's manual - (English)
- 88 Series 2 Brochure - (English)
- Elm Street School, Gardner MA - (English)
- Beckett (CG10, CG25, CG50) 550-142-027 - (English)
- Beckett 550-142-026 - (English)
- Carlin 550-142-030 - (English)
- Power-Flame (WJ30A, WJ50A) 550-142-028 - (English)
- Power-Flame WCR 550-142-029 - (English)
- Riello RL 550-142-024 - (English)
- Riello RLS 550-142-023 - (English)
- Riello RS 550-142-025 - (English)
- Webster (WJB1, WJB2) 550-142-022 - (English)
- Model 88 Warranty Residential - (English)
- Models 88 Warranty Commercial - (English)
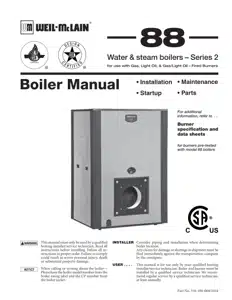
- Before installing boiler
- Set boiler in place
- Assembling the block
- Perform hydrostatic pressure test
- Complete block assembly
- Connect water boiler piping
- Connect steam boiler piping
- Install jacket
- Pipe tankless heaters
- Install water boiler controls
- Install steam boiler controls
- Connect breeching and venting systems
- Connect breeching and venting systems
- Install burner & wiring and fill system
- Install fuel piping
- Make final adjustments
- Dimensions
- Parts
- Weil-McLain® Cast Iron Gas Boiler and Oil Boiler
Table of contents
User Manual Weil-McLain 88 SERIES 2 COMMERCIAL GAS OIL BOILER
Before installing boiler
Installation must comply with —
- State, provincial and local plumbing, heating and electrical codes.
- Regulations of servicing utilities.
- ASME Section IV, Low Pressure Boiler and Pressure Vessel Code.
- National Fuel Gas Code, ANSI/NFPA 54 - latest edition, when applicable.
- National codes where applicable.
Before selecting boiler location
1. Check for nearby connections to:
a. Fuel supply.
b. Electrical power.
c. System water or steam piping.
d. Venting systems - see page 29.
e. Combustion and ventilation air supply — see page 5.
2. Check area around boiler. Remove any combustible materials, gasoline and other flammable vapors and liquids.
WARNING:Failure to keep boiler area clear and free of combustible materials, gasoline and other flammable liquids and vapors can result in severe personal injury, death and substantial property damage.
Provide clearance around boiler
1. Provide minimum clearances to combustible materials:
- Boiler top — 24 inches.
- Boiler front — 48 inches.
- Boiler flue — 9 inches.
- Boiler rear — 9 inches.
- Boiler sides — 6 inches.
- Single-wall vent pipe – 18 inches.
- Double-wall vent pipe – refer to vent pipe manufacturer's recommendations for vent pipe clearances.
2. Boiler may be installed on combustible flooring.
3. See page 36 for boiler dimensions.
NOTICE: Flue pipe/breeching clearances take precedence over jacket clearances.
4. Provide minimum clearances for servicing:
- Left side — for cleaning and tankless heater removal – inches.
- Rear — for breeching — 36 inches.
- Allow sufficient space on remaining sides for cleaning, servicing and burner installation. See burner literature for length and recommended service clearances.
Lay a foundation, if needed
1. Floor construction and condition must be suitable for weight of boiler when filled with water. See page 35 for approximate boiler operating weight.
2. A level concrete or brick foundation, constructed per Figure 1 and Figure 2 is required when:
a. A floor could possibly become flooded.
b. Non-level conditions exist.
Figure 1 Boiler foundation, when required
Figure 2 Boiler foundation (see Figure 1)
Combustion and ventilation air openings
Combustion air openings to inside
Required volume of interior spaces
ANSI/NFPA 54 allows combustion air to be supplied through openings to interior spaces if the volume of the connected interior spaces meets the minimum volume required by the standard.
The minimum volume of interior spaces can be taken as 50 cubic feet per Btuh of all appliances in the spaces, or the minimum volume can be calculated using the formulas given in ANSI/NFPA 54- latest edition. Exception: If the air infiltration rate for the spaces is known to be less than 0.40 air changes per hour, the minimum volume must be calcu- lated as specified in the standard.
Inside air opening sizes and locations
For spaces that provide the minimum volume required by ANSI/NFPA 54, the air openings must be sized per the following:
Combining spaces on the same story — Each opening shall have a minimum free area of 1 in2 Btuh (2200 mm2 kW) of the total input rating of all appliances in the space but not less than 100 in2 One opening shall commence within 12 inches (300 mm) of the top, and one opening shall commence within 12 inches (300 mm) of the bottom, of the enclosure. The minimum dimension of air openings shall be not less than 3 inches (80 mm).
Combining spaces in different stories — The volumes of spaces in different stories shall be considered as communicating spaces where such spaces are connected by one or more openings in doors or floors having a total minimum free area of 2 in2 /1000 Btuh (4400 mm2 /kW) of total input rating of all appliances.
Figure 3 Combustion and ventilation air openings - Boiler room below grade
Figure 4 Combustion and ventilation air openings - Boiler room partially or completely above grade
Combustion air openings to outside
Outdoor combustion air can be taken through per- manent openings (TWO or ONE), as described in the following. The minimum dimension of air openings shall not be less than 3 inches (80 mm).
Outside openings: TWO permanent openings method
Two permanent openings, one commencing within inches (300 mm) of the top and one commencing within 12 inches (300 mm) of the bottom of the enclo- sure shall be provided. The openings shall communicate directly, or by ducts, with the outdoors or spaces that freely communicate with the outdoors, as follows:
- Where directly communicating with the outdoors or where communicating to the outdoors through vertical ducts, each opening shall have a minimum free area of 1 in2 Btuh mm2 kW) of total input rating of all appliances in the enclosure.
- Where communicating with the outdoors through horizon- tal ducts, each opening shall have a minimum free area of in2 Btuh (1100 mm2 kW) of total input rating of all appliances in the enclosure.
Outside openings: ONE permanent opening method
One permanent opening, commencing within 12 inches (300 mm) of the top of the enclosure, shall be provided. The appliance shall have clearances of at least 1 in. (25 mm) from the sides and back and 6 inches (150 mm) from the front of the appliance. The opening shall directly communicate with the outdoors or shall communicate through a vertical or horizontal duct to the outdoors or spaces that freely communicate with the outdoors and shall have a minimum free area of the following: in2
- Btu/hr (700 mm2 per kW) of the total input rating of all appliances located in the enclosure, and . .
- Not less than the sum of the areas of all vent connectors in the space.
Combustion air — combination indoor and outdoor openings
ANSI/NFPA 54 allows combustion air to be taken from a combination of openings to outside and to interior spaces. Follow all requirements of the standard to determine the minimum volume of interior spaces and to calculate minimum sizes of openings.
Engineered Installations
Engineered combustion air installations shall provide an adequate sup- ply of combustion, ventilation, and dilution air and shall he approved by the authority having jurisdiction.
Mechanical Combustion Air Supply
Where all combustion air is provided by a mechanical air supply system, the combustion air shall be supplied from outdoors at the minimum rate of 0.35 ft3 minute per Btuh (0.034 m3 min per kW) for all appliances located within the space.
- Where exhaust fans are installed in the building, additional air shall be provided to replace the exhausted air.
- Each of the appliances served shall be inter- locked to the mechanical air supply system to prevent main burner operation where the me- chanical air supply system is not in operation.
- Where combustion air is provided by the build- ing’s mechanical ventilation system, the system shall provide the specified combustion air rate in addition to the required ventilation air.
Louvers, Grilles, and Screens.
The required size of openings for combustion, venti- lation, and dilution air shall be based on the net free area of each opening.
Where the free area through a design of louver or grille or screen is known, it shall be used in calculating the size opening required to provide the free area specified.
Where the louver and grille design and free area are not known, it shall be assumed that wood louvers will have percent free area, and metal louvers and grilles will have 75 percent free area.
Non-motorized louvers and grilles shall be fixed in the open position.
Minimum screen mesh size
Screens shall not be smaller than 1⁄4 inch mesh.
Motorized louvers
Motorized louvers shall be interlocked with the appli- ance so they are proven in the full open position prior to main burner ignition and during main burner opera- tion. Means shall be proved to prevent the main burner from igniting should the louver fail to open during burner startup, and to shut down the main burner if the louvers close during burner operation.
Set boiler in place
WARNING: Ensure the equipment and cables used for lifting are designed to handle the load. See Figure 5 for approximate weights of model 88 section assemblies. Failure to comply can result in severe personal injury, death or substantial property damage.
NOTICE: Cables used for lifting are NOT provided by Weil-McLain.
For packaged boiler:
1. Remove top jacket panels. Set aside until after boiler is piped.
WARNING: The boiler contains ceramic fiber and fiberglass materials. Use care when handling these materials per instructions on "Handling ceramic fiber and fiberglass materials," page 34 of this manual. Failure to comply could result in severe personal injury.
2. Remove lag screws (2 in front, 2 in rear) from shipping rails.
3. Remove boiler from skid. See Figure 5 for lifting weight.
- Using crane — hook middle of each cable to eye of crane.
- Using hoist — hook middle of each cable to hoist. Raise boiler off skid. Use pipe rollers under skid angles to roll boiler.
4. Place boiler in final position. Center boiler on foundation, if used.
5. Level boiler. Shim under skid angles, if necessary.
6. Cut off cables.
WARNING: Cables are not intended for long-term usage. Cables may cor- rode inside boiler, weakening their lifting strength. Failure to remove cables can result in severe personal injury, death or substantial property damage.
7. Proceed to "Perform hydrostatic pressure test," page 11.
For block assembly:
1. Remove lag screws (2 in front, 2 in rear) from shipping rails.
2. Remove boiler from skid. See Figure 5 for lifting weight.
- Using crane – attach free end of cables to eye of crane.
- Using hoist – attach free end of cables to hoist. Raise boiler off skid. Use pipe rollers under steel skid angles to roll boiler.
3. Place boiler in final position. Center boiler on foundation, if used.
4. Level boiler. Shim under skid angles, if necessary.
5. Cut off cables.
WARNING: Cables are not intended for long-term usage. Cables may cor- rode inside boiler, weakening their lifting strength. Failure to remove cables can result in severe personal injury, death or substantial property damage.
6. Inspect block assembly for disjointed sections. Check gas-tight seal of flue collector hood and clean out plates.
Figure 5 Section assembly lifting weights
WARNING: Gas tight seal must be maintained to pre- vent possible flue gas leakage and carbon monoxide emissions, resulting in severe personal injury or death.
a. Check inside section assembly for any light passing through unsealed areas.
b. Mark all unsealed areas.
c. At unsealed areas, check for:
- Damaged gaskets.
- Sealing rope not in place.
- Loose bolts or nuts.
d. Correct all conditions and repeat step b. If un- sealed areas still exist, contact your Weil-McLain distributor or sales office before continuing installation.
7. Proceed to "Perform hydrostatic pressure test," page 11.
Assembling the block
Prepare and position back section
1. Apply 1 continuous bead of sealing rope adhesive in seal- ing rope grooves. See Figure 6. Do not get any adhesive on machined port surfaces.
2. Place 1⁄2" sealing rope in groove. Around curves, grasp at 1" intervals and push together. Do not stretch.
WARNING: Do not pre-cut rope. Gas tight seal must be main- tained to prevent possibility of flue gas leakage and carbon monoxide emissions, causing severe personal injury or death. Cut rope as each section is completed.
3. Remove any grit from port machined surfaces with clean rag.
WARNING: Do not use petroleum-based cleaning or sealing compounds in boiler system. Severe damage to system components can result, causing substantial property damage.
4. Place 9" and 6" sealing rings in appropriate port openings. See Figure 6. If sealing ring slips out of groove, stretch ring gently for several seconds, then reposition in groove.
5. Apply continuous bead of silicone sealant no larger than 1 around entire outside edge of outer machined surface of port. Refer to Figure 7. Do not apply silicone sealant on, next to or under sealing ring.
WARNING: Silicone sealant applied as specified above prevents unburned oil vapors from coming in contact with sealing ring. Vapor contact can damage rings, re- sulting in severe damage to boiler and substantial property damage.
6. Hoist back section upright. Then temporarily screw a 6-inch threaded pipe at least 36 inches long into the lower (return) tapping.
7. Hoist the section and put into position.
8. Place a block under the 6-inch pipe to hold the back section upright and plumb.
CAUTION: The back section must be plumb before installing other sections to ensure the block will assemble correctly.
9. The 6-inch support pipe and block can be removed after several sections have been installed, and the assembly is stable.
10. Install intermediate sections as described on the following page.
Figure 6 Sealing rope installation
Figure 7 Silicone sealant
Install intermediate sections
1. Remove and discard 3 diameter shipping tie rods.
2. Remove grit from port machined surfaces with clean rag.
WARNING: Do not use petroleum-based cleaning or sealing compounds in boiler system. Severe damage to system components can result, causing substantial property damage.
3. Position intermediate section so aligning lugs fit into sockets of next section. See Figure 8.
4. Install TI (tankless intermediate) and SI (supply intermediate) sections (when used) in order shown in Figure 9, page 10.
5. Draw sections together until metal-to-metal contact is made around machined port openings (see Figure 8):
a. Oil threads on 4 draw rods. Install washer and nut on end to be tightened. Use nut only on other end.
b. Uniformly draw sections together, starting at washer/nut end.
NOTICE: Important — Leave an equal amount of thread on each end of the draw rod. This is needed to allow securing the jacket support brackets in place.
c. Draw rods should be torqued to a range of 100 to 120 ft-lbs. Do not back off draw rods.
d. Metal-to-metal contact will be achieved around port open- ings. See Figure 8. If gap occurs, it should be no greater than Check with feeler gauge.
e. If, for any reason, gap around machined port opening ex- ceeds .032", check for rope extending from rope grooves, dirt on port openings or sockets, or misaligned lugs. If correc- tions are made and gap still exists, contact your Weil-McLain distributor or sales office before continuing installation.
Figure 8 Sealing ring installation and port alignment
CAUTION: After erecting first intermediate section, check both sections for plumb. Failure to plumb sec- tions can cause misaligned piping and breech- ing, possibly resulting in property damage.
6. Repeat steps 1-5.
7. Check each section for proper sealing rope position before proceeding to next section.
WARNING: Failure to position sealing rope properly can cause boiler to not seal gas-tight. Gas tight seal prevents possible flue gas leakage and carbon monoxide emissions, resulting in severe per- sonal injury or death.
8. Install remaining intermediate sections and front section using the same procedure.
If using tankless heater (TI) sections
- Install tankless heaters and gaskets or heater cover plates and gaskets. Use 3 /8" x 3/4" studs, washers and nuts.
Figure 9 Section arrangement
Perform hydrostatic pressure test
Prepare boiler and test:
1. See Figure 10 and Figure 11 for tapping locations. Install:
a. Boiler drain (not furnished).
b. Water pressure gauge — for test only. Be sure gauge can handle test pressure — see step 3.
c. Air vent in upper tapping (K).
2. Plug remaining tappings.
CAUTION: Do not pressure test with any control installed. Damage to control can occur due to overpressure.
3. Fill boiler. Vent all air. Pressure test at least 10 minutes at a pressure not less than the following:
a. Steam boiler: Between 45 and 55 psig.
b. Water boiler: 11⁄2 times maximum allowable working pres- sure (MAWP) stamped on the boiler nameplate, located on boiler jacket front panel.
CAUTION: Do not exceed above test pressures by more than 10 psig.
WARNING: Do not leave boiler unattended. Cold water fill could expand and cause excessive pressure, resulting in severe personal injury, death or substantial property damage.
4. Check for maintained gauge pressure and leaks. Repair if found.
WARNING: Leaks must be repaired at once. Failure to do so can damage boiler, resulting in substantial property damage. Do not use petroleum-based cleaning or sealing compounds in boiler system. Severe damage to system components can result, causing substantial property damage.
5. Drain boiler and remove air vent, boiler drain and gauge. Remove plugs from tappings that will be used for controls and accessories.
Figure 10 Boiler tapping locations and sizes (see Figure 11)
Figure 11 Boiler tappings
Complete block assembly
Install burner mounting plate on front section
1. Install four (4) 1⁄2" x 31⁄2" studs to secure burner mounting plate to section:
2. Install burner mounting plate:
Install observation port assemblies on front and back sections
1. Install front observation port assembly:
2. Repeat above steps for back observation port assembly.
Install the combustion chamber blanket insulation
WARNING: The boiler contains ceramic fiber and fiberglass materials. Use care when handling these materials per instructions on page 34 of this manual. Failure to comply could result in severe personal injury.
- Remove any debris from inside the combustion chamber, leaving the combustion chamber as clean as possible.
- Apply waterglass to the bottom and left side of the combus- tion chamber (see drawing below for dimensions). Starting from the rear of the combustion chamber, unroll the com- bustion chamber blanket covering the bottom and left side as you work your way to the front of the boiler.
- Cut off combustion chamber blanket 2-1/2” back from burner opening. Discard cut off piece.
- Apply 1/8” continuous bead of sealing rope adhesive in seal- ing rope groove.
- Position rope in groove, overlapping ends at least 1”. Cut off excess rope and discard.
Figure 12 Combustion chamber blanket location
Insert HXT-bars
1. See Figure 13, page 13.
2. Flue HXT-bars are identified by painted ends. They must be inserted as shown, with the HXT-bars in the sequence:
- Top position
- red-tipped, HXT-bar 24 inches long — place on the top row of pins.
- Middle position
- white-tipped HXT-bar, 26 inches long — place on the first row of pins below the top clean-out plate boss.
- Bottom position
- blue-tipped HXT-bar, 34 inches long — place on the first row of pins below the bottom clean out plate boss.
NOTICE: DO NOT insert a bottom HXT-bar into the open- ing between the FRONT section and the first intermediate section.
3. To remove flue HXT-bars when required to clean the boiler flueways, grab the end of each HXT-bar with pliers and pull straight out. Clean HXT-bars and replace as shown in Figure 13, page 13.
Figure 13 Insert HXT-bars through clean out openings as shown below (omit the bottom, blue-tipped, HXT-bar in the opening between the front section and the first intermediate section)
Install clean out plates
WARNING: Clean out plates must be installed gas-tight to prevent possibility of flue gas leakage and carbon monoxide emissions, resulting in severe personal injury or death.
Install draft hood collar
Figure 14 Clean out plate assembly
Connect water boiler piping
General water piping information
1. System water supply and return piping should be installed and piping connections attached to boiler before erecting jacket or installing controls.
2. Do not pipe in through supply and out through return. This creates reverse water flow through boiler that must not be used.
3. When installing in a system in which return water temperature can drop below 140°F, apply the by-pass piping with by-pass pump as shown in .
Install piping
Install piping as shown in Figure 15, page 14 and Figure 19, page 15 if applicable) for single boilers. For multiple boilers, see Figure 20, page 15.
WARNING: Improperly piped systems or undersized piping can contribute to erratic boiler operation and possible boiler or system damage.
1. Connect supply and return piping:
a. Size according to tables below.
- For known flow rates or higher flow rate (less than 20°F temperature rise) through boiler, see Figure 16.
- For unknown flow rates, size piping per Figure 18, page 15, using 20°F temperature rise through boiler.
WARNING: Flow at higher rates than shown in the tables in this manual for given pipe sizes can damage the boiler, caus- ing substantial property damage.
b. Locate circulator in supply piping.
c. For return piping, use full diameter pipe for 10 times that diameter before making any reduction. For example, a 4-inch return should not be reduced any closer to boiler return tap- ping than 40 inches.
d. Install system blow-off (drain) valve in lowest part of return piping close to boiler. ASME minimum size requirements are given in Figure 18, page 15.
2. Install expansion tank:
a. Closed type – connect to 1" tapping "K" (see page 11). Use NPT piping. Any horizontal piping must pitch up toward tank at least 1 inch per each 5 feet of piping.
b. Diaphragm type – Refer to tank manufacturer's literature for location. Install automatic air vent in "K" tapping.
c. Connect cold water fill to expansion tank piping. Figure 15 shows typical piping when using a closed type tank. Connect to the same location as the expansion tank connects to the system when using a diaphragm type tank.
d. Also shown are recommended valves and water meter, when used. Water meter will detect added make-up water, indicating leaks in system.
Figure 15 Water boiler piping, typical
Figure 16 Recommended minimum pipe sizes for known flow rates (note 1)
Figure 17 Recommended minimum pipe sizes when flow rate is not known (see Figure 15, page 14) (note 1)
Figure 18 ASME blowoff/drain valve size
Piping multiple boilers
- See Figure 19. (Expansion tanks, relief valves and other accessories are required, but omitted from the illustration for simplicity.)
- The boiler piping circuits are referred to as the secondary circuits in the following.
- The legend for Figure 19 and boiler pump sizing recommenda- tions follow:
A Size boiler pump GPM based on the following:
a Temp rise = Operating limit temp – Return water temp
c. Calculate only secondary (boiler) piping circuit resistance. Al- low for head loss through the boiler equal to three 90 degree elbows of secondary pipe size.
d. Operate each boiler and its pump with a Weil-McLain boiler control panel.
e. Size secondary (boiler) circuit piping using the flow rate ranges given in Figure 18, page 15.
B Primary pump GPM and head calculation should not include secondary boiler circuits. Primary pump can operate continuously during heating season.
C Connection to primary circuit — Space 12" maximum or as close as practical.
D Check valve.
E Hand valve.
Figure 19 By-pass piping for return water less than 140°F
Figure 20 Multiple water boiler piping
Connect steam boiler piping
General steam piping information:
1. Hartford loop piping arrangement and wet return are required for steam boilers. Use the Hartford loop for both pumped-return and gravity-return systems.
2. Maintain 24-inch minimum from waterline to bottom of header from bottom of section).
3. When using condensate receiver, feed pump must be energized by boiler-mounted pump controller.
4. Install piping:
a. Install piping as shown on page 17 through page 18 for single boilers. See page 19 for additional requirements when piping multiple boilers.
b. Return pipe sizing.
- Pumped return — Size return piping by pump.
- Gravity return — Size gravity return same as Hartford loop equalizer pipe size.
c. Drain valve — Install system drain valve in lowest part of return piping close to boiler. See Figure 18, page 15, for sizing.
d. Cold water fill piping — Connect cold water fill piping as shown in Figure 21. Also shown are recommended valves and water meter, if used. Water meter will detect added makeup water, indicating leaks in system.
e. Condensate return piping:
- Satisfactory operation of any steam heating system depends on adequate return of condensate to maintain steady water level.
- Avoid adding excessive amounts of raw make-up water.
- Where condensate return is not adequate, a low water cutoff with pump control, condensate receiver, and condensate boiler feed pump should be installed.
- See Figure 22 for piping and Figure 23 for sizing.
Figure 21 Cold water fill piping
Figure 22 Condensate piping to boiler
Figure 23 Condensate receiver capacity required
CAUTION: Improperly piped systems or undersized piping can contribute to erratic boiler operation and possible boiler or system dam- age. Piping system must be installed as shown, using pipe sizes shown. Pipe sizes shown are for two-pipe, pumped-return systems. Adjust pipe sizing as needed when connecting to gravity-return systems. Consult local Weil-McLain distributor or sales offi ce before installing alternate piping.
Steam boiler piping guidelines
Minimum height of header above water line must be inches
WARNING: The boiler header must always be at least 24 inches above the water line, as shown in all steam boiler piping diagrams. Installing the pipe lower will result in increased water car- ryover to the system, resulting in potential serious damage to system components and oxygen corrosion due to excess make-up water.
NOTICE: Near boiler piping must be as shown in Figure 25 . Th e near boiler pipe may be welded between the needed threaded joints. A threaded joint may not be replaced by a welded joint. Th e steam supply must be supported to allow move- ment.
Hartford loop piping for all steam boilers
1. You must install the system supply pipe between the equalizer elbow and the last boiler riser pipe connection to the header. This assists in separating water from the steam as it turns upward into the steam supply pipe.
2. Locate the top of the Hartford loop return nipple at least 4 inches below the water line, as shown.
Figure 24 Model 488 through 688 steam (1 riser)
Figure 25 Model 788 through 1188 steam (2 risers required)
Figure 26 Model 1288 through 1888 steam (3 or 4 risers required)
Figure 27 Multiple Steam Boiler Piping Gravity Condensate Return
A Pipe as shown for gravity return systems, connecting point A to the wet gravity return.
- For pumped-return systems, install boiler water level control on each boiler with body mark at level indicated in Figure 44, page 28 . Provide at point A either:
- Separate feed pumps and check valves for each boiler, or
- Single feed pump, with separate solenoid valve for each boiler.
B For pumped-return systems, install a combination fl oat and thermostatic trap on each boiler to prevent fl ooding of one boiler while other boiler is fi ring. Install trap in skim tapping see Figure 41, page 27 ). Connect traps to condensate receiver.
- Gravity-return systems are self-levelling if the wet returns are piped to the common system wet return.
C Install boiler piping as shown in the preceding pages of this manual.
D Install stop valves per ASME code requirements.
- For pump-return systems, if using automatic steam valves, use only slow-opening automatic valves. Use a Weil-McLain Boiler Control System (such as a BCP panel) to open each steam valve automatically before fi ring burner.
E Construct common supply drop header with pipe size at least same size as largest boiler header size.
F Use:
- A Weil-McLain Boiler Control System (such as a BCP panel) with header-mounted pressure control(s) to sequence boilers, or . . .
- A steam pressure controller.
G Install drip line in common supply drop header.
- Gravity-return: Pipe drip line to wet return.
- Pumped-return: Use combination fl oat and thermostatic trap and drain to condensate receiver.
Install jacket
Before installing jacket
WARNING: The boiler contains ceramic fiber and fiberglass materials. Use care when handling these materials per instructions on page 34 of this manual. Failure to comply could result in severe personal injury.
1. These parts must be on boiler:
2. These parts may be on boiler:
a. Burner mounting plate
3. These parts must be off boiler:
Remove jacket parts from cartons
- Locate jacket cartons.
- Remove jacket parts from cartons as needed. Leave in cartons as long as possible to avoid damage.
- Jacket parts are in the boxes listed below:
Install support brackets/channels
1. Place upper and lower support brackets over draw rods as shown in Figure 30, page 21. Place the brackets on the sections as given in Figure 28. Sections are numbered from front to back.
2. Fasten each bracket loosely using two 5/8" nuts screwed onto the ends of the tie rods as shown.
NOTICE: Models 488 through 988 do not require lower support brackets. Only upper brackets are required.
Fasten all nuts and screws loosely during assembly to allow adjustment after all jacket frame parts are installed.
Figure 28 Place support brackets as listed below
3. Attach the upper channels to the upper supports as shown in callouts , and , Figure 30, page 21. Use two #10 x 1⁄2" screws at each bracket. Models 988 and larger have two-piece channels.
- The side channels are labelled A and B in Figure 30. Figure 29 gives the lengths of the side channel parts for each model.
- The channels at the boiler front and rear are part numbers 426400030 & 426400031, respectively.
Figure 29 Upper and lower side channel lengths
4. Attach the four jacket corners to the upper channels as shown in callout , Figure 30, page 21. Corner part numbers are: 426400054 (front left), 055 (front right), back left), and 057 (back right).
5. Attach the lower side, front and rear channels to the jacket corners as shown in callouts and of Fig- ure 30, page 21. Models 1088 and larger have two-piece side channels. The channels are labelled A and B in Figure 30. Figure 29 gives the lengths of these parts for each model. Front and rear lower channels are part numbers 426400032 and 426400033.
Figure 30 Installing jacket support brackets, support channels and corners (piping and other components omitted for clarity)
Install jacket front and back panels
- Slide the jacket front and back panels down over the top channels and into the bottom channels as shown in Figure 32 .
- Slide the upper and lower channels as needed to square up the fi t.
Install jacket side panels
1. Remove jacket side panels from cartons.
2. Before installing side panels, square up the jacket support rails.
- Place any of the jacket side panels on the rails as shown in Figure 32 .
- Butt the side panel against the jacket corner panel.
- Push/pull on the upper and lower channels until the fi t-up of the side panel, corner panel and channels is square.
- Place a jacket top panel in position against the jacket front panel to ensure the top alignment is square. Adjust the jacket support rails forward or backward if needed for square alignment.
- Tighten the 5/8-inch nuts on the upper (and lower) support brackets.
- Tighten the screws securing the upper and lower rails to the sup- port brackets.
- Tighten the screws securing the front and back panels to the rails.
3. Apply all jacket side panels in the order shown in Figure 34 .
- Remove jacket knockouts as required for tankless heaters and tank- less heater openings.
- Note that panel sequence is not important for boilers not equipped with tankless heater intermediate sections.
Install top insulation
WARNING: The boiler contains ceramic fi ber and fi berglass materials. Use care when handling these materials per instructions on page 34 of this manual. Failure to comply could result in severe personal injury.
- Cut insulation to length.
- Center and align front and back of insulation to outside edges of front and back sections.
- Center insulation on top of sections, and fold sides of insulation until folded sides of insulation compress between section and top mount- ing brackets.
Figure 31 Installing top insulation
Install jacket top panels
1. Place jacket top panels as shown in Fig- ure 35, page 24 .
- Remove knockouts for riser pipes and air bleed piping (front section) using tin snips.
Install jacket trim
2. Press jacket trim down over the front and side jacket panels as shown in Figure 33 .
Figure 32 Installing (removing) jacket front, rear and side panels
Figure 33 Press jacket trim down over jacket front, rear and side panels
Figure 34 Jacket side panel placement
Figure 35 Jacket top panel placement
Pipe tankless heaters
To pipe tankless heaters:
1. Size piping no smaller than heater inlet and outlet.
2. Automatic mixing valve must be installed. See Figure 37. Follow manufacturer's instructions to install.
3. Flow regulating valve must be installed. Size according to con- tinuous draw of heater. See Figure 36. Follow manufacturer's instructions to install.
4. Operating control with small adjustable differential scale is recommended. Install in temperature control tapping in heater plate.
5. Multiple tankless heaters (see Figure 37):
a. Use cold water supply header with individual risers to each heater. Size header by increasing one pipe size for each additional heater.
b. Use hot water outlet header with individual risers to each heater. Size header by increasing one pipe size for each additional heater.
c. Do not pipe multiple heaters in series.
6. In hard water areas, soften cold domestic water supply to heat- ers to prevent lime build-up.
Figure 36 Tankless heater ratings (Weil-McLain ratings)
Figure 37 Tankless Heater Piping
Install water boiler controls
Install controls
1. Install furnished controls per Figure 39 and Figure 38.
WARNING: Failure to properly install, pipe and wire boiler controls can result in severe damage to boiler, building and per- sonnel; and is not covered by boiler warranty.
2. Relief valve must be installed with spindle in vertical position. Use fittings provided with boiler. Do not make any other connection in that piping.
WARNING: Relief valve discharge line must be piped using rigid material suitable for 375°F, threaded one end, near floor close to drain to eliminate potential of severe burns. Do not pipe to any area where freezing could occur. Do not plug, valve or place any obstruction in discharge line.
3. When installing low water cut-off
a. Must be installed if boiler is located above radiation level.
b. May be required on water boilers by certain state, local or ter- ritorial codes or insurance companies.
c. Install low water cutoff designed for water installations where shown in Figure 39 and Figure 38.
4. If installation is to comply with ASME installation requirements, an additional high temperature limit is needed. Purchase and install in supply line between boiler and isolation valve or in tapping "A."
5. Dual limit control settings: a Low – set according to design requirements. b High – at least 20° higher than low limit, 240°F maximum.
6. Install optional controls per control manufacturer's instructions.
Figure 38 Water control locations
Figure 39 Water control tappings (see Figure 38)
Install steam boiler controls
Install controls:
1. Install controls where shown in Figure 40 and Figure 41.
WARNING: Failure to properly install, pipe and wire boiler controls can result in severe damage to boiler, building and per- sonnel; and is not covered by boiler warranty.
a. Install steam pressure operating and high limit controls and pressure gauge. See Figure 40, Figure 41 and Figure 42, page 28. Pressure limit control settings:
- Low – set according to design requirements.
- High – set at least 2 psi higher than low limit, 15 psi maxi- mum.
b. Relief valve must be installed with spindle in vertical position. Use fittings provided with boiler. Do not make any other con- nection in that piping.
WARNING: Pipe relief valve discharge through vertical piping to at- mosphere. Use rigid material suitable for 375°F, threaded one end only. Install drain pan elbow to drain condensate. Pipe near floor close to floor drain to eliminate potential of severe burns. Do not pipe to any area where freezing could occur. Do not plug, valve or place any obstruction in discharge line.
c. Install water level controls and gauge glass per Figure 40, Figure 41 and Figure 44, page 28.
- Fittings for controls to be furnished by others.
- If water level control is not shown in Figure 43, page 28, locate casting mark on control and install per manufac- turer's instructions.
NOTICE: Do not use water level controls with quick hook-up fit- tings. Nuisance shutdowns will occur.
Figure 40 Steam control tappings (see Figure 41)
Figure 41 Steam control locations
Figure 42 Steam control siphon and fittings
Figure 43 Float-type water level control locations
Figure 44 Water level control locations (see Figure 43)
Connect breeching and venting systems
General venting information
1. Model 88 boilers operate with positive overfire pressure. Adjust damper assembly (see Figure 51, page 33) during burner start- up to achieve 0.1" W.C. positive pressure at damper sample hole.
Select type of venting system
Forced draft
- Boiler, breeching and stub vent operate at positive pressure. En- tire system must be gas-tight to prevent leaks. Stub vent height must be limited to prevent negative draft with 3-foot minimum stub vent height above roof. See Figure 46 and Figure 48.
Balanced draft
- Boiler operates with positive pressure overfire. Chimney may provide excess draft which may require a barometric draft control installed and set to provide minimum draft to maintain positive pressure at flue collar. Minimum chimney height above roof is 3 feet. See Figure 47 and Figure 49.
Construct metal breeching:
1. See Figure 45 for minimum breeching diameter.
2. Select material type and thickness in compliance with local codes.
WARNING: Conventional flue pipe should not be used as it could leak flue gases and carbon monoxide emissions through seams and joints, resulting in severe personal injury or death.
3. Refer to ASHRAE Guide for chimney and breeching calculations and construction and lining.
WARNING: Long horizontal breechings, excessive number of tees and elbows or other obstructions restricting combus- tion gas flow can result in possibility of condensation, flue gas leakage and carbon monoxide emissions, causing severe personal injury or death.
Figure 45 Minimum breeching diameter
Connect breeching and venting systems
Figure 46 Stub vent – forced draft — single boiler
Figure 47 Conventional chimney – balanced draft with barometric draft control when required — single boiler
Figure 48 Stub vent – forced draft — multiple boilers
Figure 49 Conventional chimney – balanced draft with barometric draft control when required — multiple boilers
Install burner & wiring and fill system
To install burner
1. Unpack burner.
2. Place gasket around air tube and against burner mounting flange. If sealing rope is used, apply 1 continuous bead of rope adhesive around burner mounting flange and apply sealing rope to make gas-tight seal.
3. Mount burner into opening in burner mounting plate.
CAUTION: Maintain gas-tight seal between burner mounting flange and plate to prevent damage to air tube.
NOTICE: If a boiler base is Not utilized, the applicable burner specification and boiler manual dimensions should be reviewed for burner height to burner opening in the boil- er. Some burner manufacturers may offer an optional inversion kit to invert the burner allowing clearance to the floor.
4. Level burner using burner support brackets where required.
5. Secure with furnished bolts.
6. Retain burner information packet. Keep with boiler.
To wire burner and boiler controls
WARNING: Electric shock hazard. Can cause severe personal injury or death if power source is not disconnected before installing or servicing boiler and burner.
1. Install all wiring in compliance with:
- National Electrical Code ANSI/NFPA 70 - latest edition.
- Any additional national, state, or local codes.
2. Follow burner manual and wiring diagram found in burner in- formation packet.
3. Use #14 AWG wire for operating and safety circuit wiring.
4. Where burner motor voltage differs from control voltage, supply proper voltage to each. Size fused disconnects and conductors per National Electrical Code ANSI/NFPA 70 - latest edition.
Determine if water treatment is needed water boilers only)
WARNINGS: Do not use petroleum-based cleaning or sealing com- pounds in boiler system. Severe damage to system com- ponents can result, causing substantial property damage.
Continual make-up water will reduce boiler life. Minerals can build up in sections, reducing heat transfer, overheating cast iron and causing section failure.
For unusually hard water areas or low pH conditions less than 7.0) consult local water treatment company. Provide a water softener for make-up water if hardness exceeds 7 grains.
Freeze protection (when used) water boilers only)
1. Use antifreeze especially made for hydronic systems. Inhibited propylene glycol is recommended.
WARNING: Do not use automotive, ethylene glycol or undiluted antifreeze. Severe personal injury or death can result.
50% solution provides protection to about -30°F.
3. Local codes may require back-flow preventer or actual disconnect from city water supply.
4. Determine quantity according to system water content. Boiler water content is listed in "Ratings," page 35. Percent of solution will affect sizing of heat distribution units, circulator and expansion tank.
5. Follow antifreeze manufacturer's instructions.
To fill water boilers
To fill steam boilers
Install fuel piping
Gas piping
1. In sizing the gas piping, the following factors should be consid- ered:
a. Diameter and length of the gas supply piping.
b. Number of fittings.
c. Maximum gas consumption (including any possible future expansion).
d. Allowable loss in gas pressure from the gas meter outlet to the boiler.
2. Minimum inlet natural gas pressure required at manual main shut- off valve — see the burner manual and material list.
3. Follow good piping practices.
4. Pipe joint compound (pipe dope) must be resistant to the corrosive action of liquefied petroleum gases and applied sparingly only to the male threads of pipe joints.
5. A ground joint union must be installed in the piping to provide for servicing. The supply piping must include a manual shut-off valve and sediment trap. See Figure 50.
6. Piping must be supported by hangers, not by the burner or its accessories.
7. Purge all air from the supply piping.
8. All gas piping must be tested for leaks after installation. Use soap suds mixture only.
Fuel oil piping
DANGER: To prevent oil flow in case of oil line breakage:
- Use anti-syphon device when any part of the oil tank is above burner level.
- Use check valve in suction line on burner side of manual shut-off valve nearest tank when top of fuel oil tank is below burner level.
Failure to comply could result in fuel leakage or fire, caus- ing potential severe personal injury, death or substantial property damage.
1. A two-pipe fuel oil piping system is required for all installations.
2. Supply and return lines must enter tank from top, extending to within 4 to 6 inches from bottom of tank.
3. Use oil filter sized for fuel pump suction gear capacity.
4. Install oil filter.
CAUTION: Do not install filter outside or close to an outside wall.
5. Use continuous copper tubing to reduce possible piping leaks and to ensure reliable seal when oil piping is buried.
6. Use flare fittings, not compression fittings.
DANGER: Fire hazard — DO NOT USE soldered fittings. No safe repair can be made.
Figure 50 Gas supply piping
7. Follow good piping practices.
8. Pipe joint compound (pipe dope) must be resistant to corrosive action of fuel oil. Apply sparingly only to male threads of pipe joints.
9. Supply and return piping should be sized to design conditions, but not less than 1⁄2" O.D. continuous copper tubing.
10. Auxiliary fuel oil pump is recommended when suction line lift exceeds 12 feet.
11. Install swing joints so they will tighten as buried tank settles to prevent fuel line breakage.
12. Where iron pipe is required by local codes, make swing joints with nipples and elbows several inches long on both suction and return line. Locate close to tank.
13. Install manual shut-off valve in suction line piping near burner and where piping enters building from outside tank.
14. Pitch suction line piping toward fuel tank.
15. Provide tee and plug at highest point in suction line to release air from suction line and aid in priming.
Make final adjustments
Adjust burner and damper assembly:
Figure 51 Flue collar/damper assembly
1. Lock flue damper OPEN (Figure 51).
WARNING: Make final burner adjustments using combustion test equipment to assure proper operation. Do not fire boiler without water. Sections will overheat, damaging boiler and resulting in severe property damage.
2. Refer to burner manual for start-up and service.
3. Let burner advance to high fire. Heat boiler to design conditions.
4. Using combustion test equipment, adjust burner for:
NOTICE: On some applications, if draft conditions or burner char- acteristics cause the burner flame pattern to impinge on the combustion chamber wall, you may notice pinging sounds from the boiler. Adjust the burner if possible to redirect the flame. If this does not work, contact your boiler supplier or Weil-McLain to obtain an optional combustion chamber kit (see page 38 for contents).
5. Adjust flue collar damper (Figure 51) to ensure 0.1" W.C. positive pressure at test opening.
6. Tighten screws to secure in position.
7. Plug test opening with 1/8" plug provided with flue collar/damper assembly.
8. Adjust barometric draft control, when used, to design condi- tions.
9. Repeat steps 4 through 6. Adjust as required.
Skim steam boilers:
NOTICE: Clean all newly installed steam boilers to remove oil. Failure to properly clean can result in violent water level fluctuations, water passing into steam mains, or high maintenance costs on strainers, traps and vents. Skim boiler only. Do not clean old piping or leaks can occur.
WARNING: Do not use petroleum-based cleaning or sealing com- pounds in boiler system. Severe damage to system com- ponents can result, causing substantial property damage.
1. Remove 2" plug from skim tapping "A" (see Figure 40, page 27).
2. Provide 2" skim piping from tapping to floor drain.
3. Raise waterline to midpoint of skim piping.
4. Fire burner to maintain temperature below steaming rate during skimming process.
5. Feed in water to maintain water level.
6. Cycle burner ON/OFF as needed to prevent rise in steam pres- sure.
7. Continue skimming until discharge is clear. This may take several hours.
8. Drain boiler.
9. While boiler is warm, but not hot, flush all inte- rior surfaces under full pressure until drain water runs clear.
10. Remove skim piping.
11. Re-insert plug at boiler skim tapping.
12. Close drain cock.
13. Fill with fresh water to normal water line.
14. Start burner and steam for 15 minutes to remove dissolved gases.
15. Stop burner.
16. Check traps and air vents for proper operation.
Check boiler for gas-tight seal:
WARNING: Boiler must be sealed gas-tight to prevent possible flue gas leakage and carbon monoxide emissions, resulting in severe personal injury or death.
1. Remove boiler jacket side and top panels.
WARNING: The boiler contains ceramic fiber and fiberglass materials. Use care when han- dling these materials per instructions on page 34 of this manual. Failure to comply could result in severe personal injury.
2. Start burner. Observe all sealing points and chalk mark any not gas-tight.
3. To seal all chalk-marked areas:
4. Reinstall all jacket panels.
Dimensions
Figure 52 Dimensions (see lettered dimensions on opposite page)
Parts
Figure 53 Parts
Weil-McLain® Cast Iron Gas Boiler and Oil Boiler
Models 80, 88, and 94
Limited Warranty for Commercial Use
Retain proof of purchase and installation date.
A. What Does This Limited Warranty Cover?
This Limited Warranty for Commercial Use covers any defects in material and workmanship in your WeilMcLain Cast Iron Gas or Oil Boiler Model 80, 88, or 94 the “Product”).
B. How Long Does The Coverage Last?
There are two separate coverage periods under this Limited Warranty: (1) the Heat Exchanger Limited Warranty Period, and (2) the Parts Limited Warranty Period. The Heat Exchanger Limited Warranty Period runs for ten years from the date your Product was installed. The Parts Limited Warranty Period runs for one year from the date your Product was installed and applies to all parts of your Product except the heat exchange
C. Who Can Make Claims Under This Limited Warranty?
This Limited Warranty is available to you if you are the original retail purchaser or a subsequent owner and the Product has been used at any time for business purposes. A Product used at all times solely for personal, family, or household purposes is covered by the Limited Warranty for Residential Use for the Weil-McLain Cast Iron Gas Boiler and Oil Boiler Models 80, 88, and 94.
D. What Will Weil-McLain Do To Correct Problems?
If Weil-McLain determines during the Heat Exchanger Limited Warranty Period that a heat exchanger section is defective in material or workmanship, then Weil-McLain will provide a replacement heat exchanger section. If Weil-McLain determines during the Parts Limited Warranty Period that any part other than a heat exchanger section is defective in material or workmanship, then Weil-McLain will provide a replacement part.
Weil-McLain will provide replacement heat exchanger sections and other parts free of charge. Weil-McLain will furnish replacement heat exchanger sections from the closest comparable boiler model available from WeilMcLain at the time of the replacement.
If Weil-McLain provides a replacement heat exchanger section, then that replacement heat exchanger section will be covered under this Limited Warranty for the time remaining in the original Heat Exchanger Limited Warranty Period. If Weil-McLain provides a replacement for any part other than a heat exchanger section, then that replacement part will be covered under this Limited Warranty for the time remaining in the original Parts Limited Warranty Period.
E. What Will Weil-McLain Not Do To Correct Problems?
Weil-McLain will not pay for the labor to remove any heat exchanger section or other part that is the subject of your warranty claim or to install replacements provided under this Limited Warranty. Additionally, Weil-McLain will not pay for the cost of any tools, repair materials, or travel necessary to perform the removal or installation.
F. What Is Not Covered Under This Limited Warranty?
This Limited Warranty does not cover any Product that has been moved from its original installation site; any components that are not supplied by Weil-McLain; and any burner supplied by Weil-McLain. (Burners supplied by Weil-McLain are covered by a separate manufacturer’s warranty.) Additionally, this Limited Warranty does not cover claims you make if the failure, malfunction, or unsatisfactory performance of, or damage to, your Product resulted from or is attributable to:
1. Inaccurate or incomplete information or data supplied or approved by any party other than Weil-McLain;
2. The failure to properly size the Product for its use;
3. Installation not done in accordance with manufacturer’s instructions;
4. Services provided by and workmanship of the installer of the Product;
5. Components that are not supplied by Weil-McLain;
6. Improper or negligent operation, adjustment, control settings, repair, care, or maintenance of the Products, or the failure to adjust, set the controls of, repair, care for, or maintain the Products;
7. Operation with combustion air contaminated by chemical vapors, with improper fuel additives, or with water conditions that have caused deterioration or unusual deposits in the heat exchanger;
8. Freezing, accident, fire, flood, or other acts of God; abuse or misuse; unauthorized alteration; or power surges or failures; and
9. Normal wear and tear.
WEIL-McLAIN’S MAXIMUM LIABILITY SHALL NOT EXCEED THE ACTUAL PURCHASE PRICE PAID BY YOU FOR YOUR PRODUCT. IN NO EVENT SHALL WEIL-McLAIN BE RESPONSIBLE FOR INDIRECT, INCIDENTAL, CONSEQUENTIAL (INCLUDING WITHOUT LIMITATION DAMAGE TO OR LOSS OF OTHER PROPERTY), OR PUNITIVE DAMAGES, WHETHER SUCH CLAIM OR ACTION IS BASED ON CONTRACT, WARRANTY, NEGLIGENCE, STRICT LIABILITY, OR ANY OTHER LEGAL THEORY. ALL IMPLIED WARRANTIES, INCLUDING MERCHANTABILITY AND FITNESS FOR A PARTICULAR PURPOSE, ARE DISCLAIMED IN THEIR ENTIRETY.
G. How Do You Make A Warranty Claim?
If you believe you have a claim under this Limited Warranty, please contact a qualified heating or plumbing contractor of your choice. Your contractor will perform a diagnosis and advise you as to whether you may have a claim covered by this Limited Warranty. If your contractor advises you that you may have a claim covered by this Limited Warranty, then the contractor will file the claim on your behalf. You must make all parts that are subject to a warranty claim available to your contractor for return to Weil-McLain. If you have questions about this process or the status of your claim, you may call the Weil-McLain Warranty Call Center at 855-627-6003.
H. How Can You Register Your Purchase?
Registration is not required to activate your warranty, but you should retain proof of purchase and installation date.
If you have any questions about your coverage under this Limited Warranty, please contact Weil-McLain using the contact information provided above
See other models: 88 SERIES 2 COMMERCIAL GAS OIL BOILER 588 88 SERIES 2 COMMERCIAL GAS OIL BOILER 488 88 SERIES 2 COMMERCIAL GAS OIL BOILER 1888 88 SERIES 2 COMMERCIAL GAS OIL BOILER 1788 88 SERIES 2 COMMERCIAL GAS OIL BOILER 1688