Loading ...
Loading ...
Loading ...
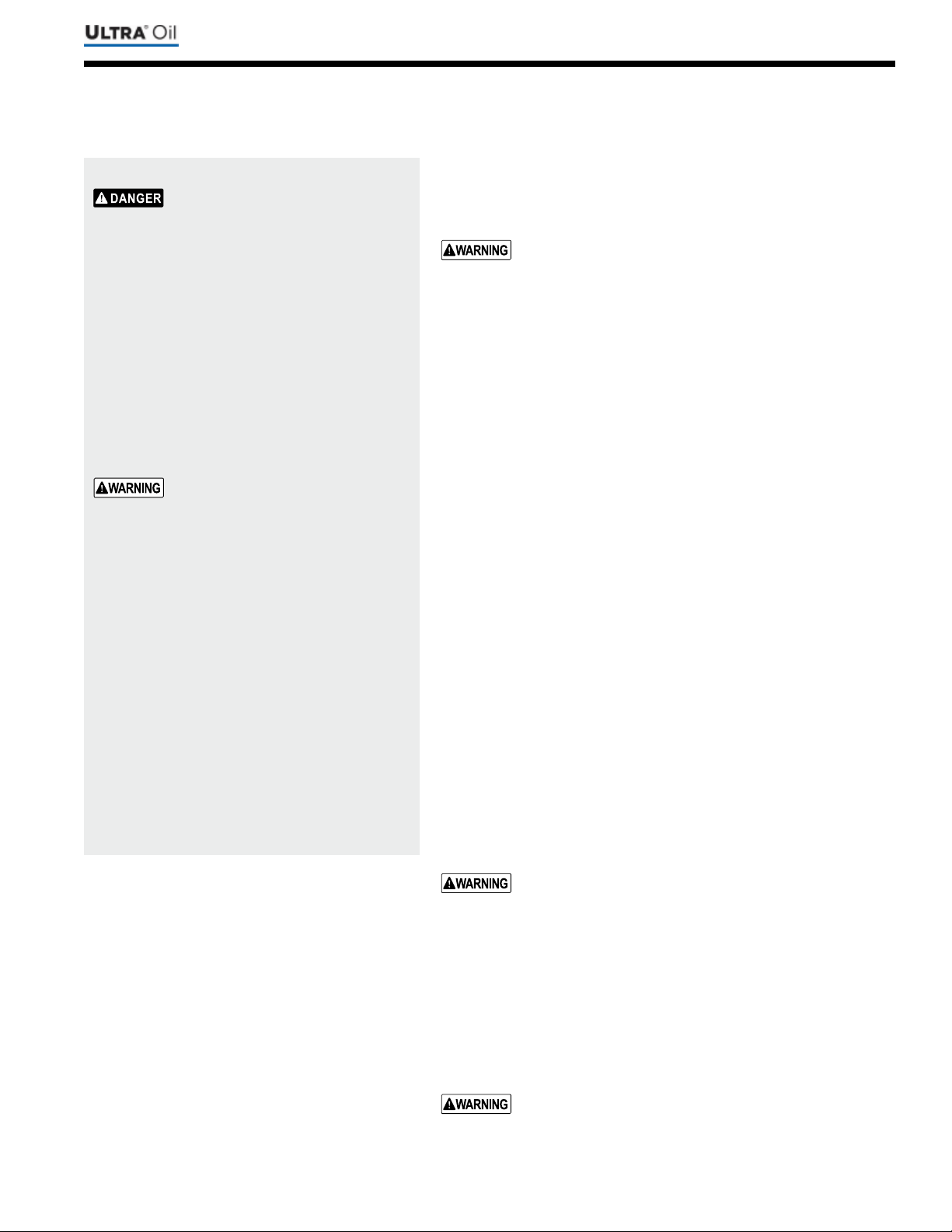
Startup procedure
• Check boiler and system piping for leaks. Continual makeup water
will reduce boiler life. Minerals can build up in sections, reducing heat
transfer and causing cast iron to overheat, resulting in section failure.
Failure to maintain recommended pH and repair leaks can
cause section iron corrosion, leading to section failure and
leaks. Do not use petroleum-based sealing or stop-leak com-
pounds in boiler systems. Damage to system components can
result.
• For pH conditions outside 7.0 to 8.5 range or unusually hard water areas
(above 7 grains hardness), consult local water treatment company.
To place in operation:
1. Verify boiler is lled with water.
2. Open burner mounting door and verify burner door insulation sections
are in proper position. Ensure the chamber oor insulation blanket is
correctly positioned.
3. Verify burner mounting door is closed tightly and burner wiring har-
nesses are connected at the jacket cross tie.
4. Factory burner adjustment and settings may not be suitable for specic
job conditions. Always use combustion test equipment to check and
adjust.
a. Follow burner manual for start-up.
b. Allow boiler to heat to design conditions.
c.
Burner should be adjusted to 13% CO
2
or less with a smoke level of
zero and breech dra of -0.01” to -0.02”. Re-adjust burner combus-
tion to account for environmental conditions. Actual CO
2
value will
vary and should be adjusted for clean and safe combustion opera-
tion. Seasonal variations as well as sucient combustion air supply
can aect proper combustion and boiler performance. e burner
should only be adjusted by a service professional with appropriate
instrumentation.
5. To observe the ame, loosen the observation port center bolt. Rotate
the observation port so the sight glass is at the 6:00 position. Retighten
the center bolt. When nished viewing, loosen the center bolt. Rotate
the observation port so the glass is at the 12:00 position. en retighten
the bolt. is will prevent soot from depositing on the glass.
Make nal burner adjustments using combustion test equip-
ment to assure proper operation. Do not re boiler without
water. Sections will overheat, damaging boiler and resulting
in substantial property damage.
5. Vent air from system. Repeat steps 4 and 5 under “Fill the system.” Air
in system can interfere with water circulation and cause improper heat
distribution.
6. Check boiler and system piping for leaks. See “Tips for water systems.”
7. Inspect breeching and venting for proper operation.
Follow additional instructions:
Read and follow the and all other instruc-
tions packed with the boiler or components.
Fill the system:
1. Close manual and automatic air vents and boiler
drain cock.
2. Fill to correct system pressure. Correct pressure will
vary with each installation. Normal cold water ll
pressure for residential systems is 12 psig. Boiler
water pH 7.0 to 8.5 is recommended.
3. Open automatic air vent one turn.
4. Open other vents.
a. Starting on the lowest oor, open air vents one at a
time until water squirts out. Close vent.
b. Repeat with remaining vents.
5. Rell to correct pressure.
Follow information below to prevent
severe personal injury, death or sub-
stantial property damage:
• Do not use gasoline crankcase drain-
ings or any oil containing gasoline. See
burner manual for proper fuel oil.
• Do not attempt to start burner when
excess oil has accumulated, when unit
is full of vapor or when combustion
chamber is very hot.
• Do not start burner unless breeching
and burner mounting door are secured
in place.
• Never burn garbage or paper in the
boiler.
• Never leave combustible material
around the boiler.
When using antifreeze — Do
not use automotive, ethylene glycol,
undiluted or petroleum-based anti-
freeze. Severe personal injury, death or
substantial property damage can result.
• Use antifreeze especially made for
hydronic systems. Inhibited propylene
glycol is recommended.
• 50% solution provides protection to
about -30 °F. Do not exceed 50% mix-
ture.
• Local codes may require back-flow
preventer or actual disconnect from
city water supply.
• Determine quantity according to sys-
tem water content. Boiler water con-
tent is listed on back cover of manual.
Percent of solution will aect sizing of
heat distribution units, circulator and
expansion tank.
• Follow antifreeze manufacturer’s in-
structions.
Part number 550-143-013/0621
23
Series 3
Loading ...
Loading ...
Loading ...