Loading ...
Loading ...
Loading ...
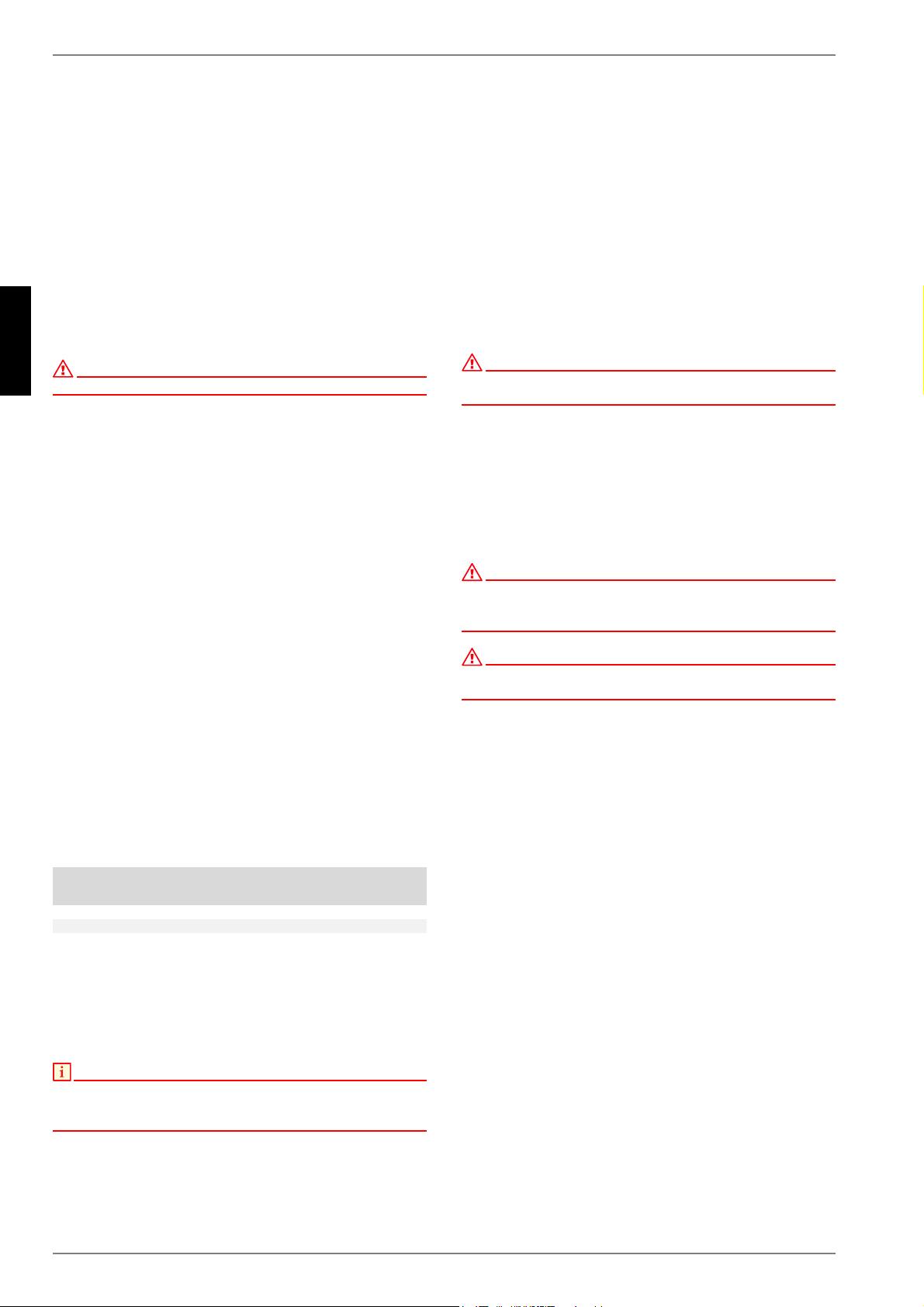
EN-6 452235.66.01 · FD 9310 www.dimplex.de
English
SI 22TU
7 Installation
7.1 General Information
The following connections need to be established on the heat
pump:
- Flow and return of the brine (heat source system)
- Flow and return flow of the heating system
- Temperature sensor
- Voltage supply
7.2 Heating System Connection
ATTENTION!
Flush the heating system prior to connecting the heat pump.
Before connecting the heating water system to the heat pump,
the heating system must be flushed to remove any impurities,
residue from sealants, etc. Any accumulation of deposits in the
liquifier could cause the heat pump to completely break down.
Once the heating system has been installed, it must be filled, de-
aerated and pressure-tested.
The sensors which are delivered already connected and loosely
placed in the switch box must be mounted and insulated accord-
ing to the block diagram.
Consideration must be given to the following when filling the sys-
tem:
Untreated filling water and make-up water must be of drink-
ing water quality
(colourless, clear, free from sediments)
Filling water and make-up water must be pre-filtered (pore
size max. 5 µm).
Scale formation in hot water heating systems cannot be com-
pletely avoided, but in systems with flow temperatures below
60 °C the problem can be disregarded.
With medium and high-temperature heat pumps, temperatures
above 60 °C can be reached.
The following standard values should therefore be adhered to
concerning the filling water and make-up water (according to VDI
2035 Sheet 1):
Minimum heating water flow rate
The minimum heating water flow rate through the heat pump
must be assured in all operating states of the heating system.
This can be accomplished, for example, by installing a dual dif-
ferential pressureless manifold.
NOTE
The use of an overflow valve is only recommended for panel heating and
a max. heating water flow of 1.3 m³/h. System faults may result if this is
not observed.
The frost protection function of the heat pump manager is active
whenever the heat pump manager and the heat circulating
pumps are ready for operation. If the heat pump is taken out of
service or in the event of a power failure, the system has to be
drained. The heating circuit should be operated with a suitable
antifreeze if heat pump systems are implemented in buildings
where a power failure can not be detected (holiday home).
7.3 Heat Source Connection
The following procedure must be observed when connecting the
heat source:
Connect the brine pipe to the heat pump flow and return. The hy-
draulic integration diagram must be adhered to.
ATTENTION!
The supplied dirt trap must be inserted in the heat source inlet of the heat
pump to protect the evaporator against the ingress of impurities.
The brine liquid must be produced prior to charging the system.
The liquid must have an antifreeze concentration of at least 25 %
to ensure frost protection down to -14 °C.
Only monoethylene glycol or propylene glycol-based antifreeze
may be used.
The heat source system must be de-aerated and checked for
leaks.
ATTENTION!
The brine solution must contain at least a 25 % concentration of a
monoethylene glycol or propylene glycol-based antifreeze, which must
be mixed before filling.
ATTENTION!
A suitable de-aerator (micro bubble air separator) must be installed in the
heat source circuit by the customer.
7.4 Temperature sensor
The following temperature sensors are already installed or must
be installed additionally:
External temperature sensor (R1) supplied (NTC-2)
Return temperature sensor (R2) installed (NTC-10)
Flow temperature heating circuit (R9) installed (NTC-10)
Flow temperature primary circuit (R6) installed (NTC-10)
Total heat
output in [kW]
Total alkaline earths
in mol/m³ and/or
mmol/l
Total
hardness in °dH
up to 200
2.0 11.2
200 to 600
1.5 8.4
> 600 < 0.02 < 0.11
Loading ...
Loading ...
Loading ...